Agir ou périr dans la jungle de la mondialisation (2° Éd.) Histoire d'une implantation Lean réussie Coll. Pro'Didakt
Langue : Français
Auteur : BICHAI Joe
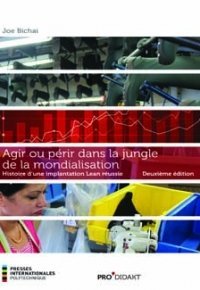
Agir ou périr dans la jungle de la mondialisation - Histoire d'une
implantation Lean réussie raconte l'aventure de la
transformation, grâce à la philosophie Lean, d'une usine désuète destinée
à la fermeture en l'usine nord-américaine la plus productive du secteur de
la chaussure.
L'ouvrage explique comment, en 10 ans, l'entreprise a éliminé les mauvaises habitudes associées à son système à flux poussé, dont le travail à la pièce, les stocks tampons, les rejets et la réparation de produits défectueux. Pour ce faire, elle a implanté le flux tendu, les modules en U fonctionnant en convergence des procédés et instauré un système de partage des gains. L'adoption par l'entreprise de la philosophie de juste à temps/Lean, combinée à des efforts kaizen, a assuré sa survie alors même que plusieurs de ses compétiteurs faisaient faillite. Mais cette transformation ne s'est pas effectuée sans embûches ni heurts. C'est ce parcours, tel qu'il a été vécu, que l'auteur relate ici avec simplicité et franchise.
L'ouvrage explique comment, en 10 ans, l'entreprise a éliminé les mauvaises habitudes associées à son système à flux poussé, dont le travail à la pièce, les stocks tampons, les rejets et la réparation de produits défectueux. Pour ce faire, elle a implanté le flux tendu, les modules en U fonctionnant en convergence des procédés et instauré un système de partage des gains. L'adoption par l'entreprise de la philosophie de juste à temps/Lean, combinée à des efforts kaizen, a assuré sa survie alors même que plusieurs de ses compétiteurs faisaient faillite. Mais cette transformation ne s'est pas effectuée sans embûches ni heurts. C'est ce parcours, tel qu'il a été vécu, que l'auteur relate ici avec simplicité et franchise.
À propos de l'auteur
Avant-propos
Remerciements
Introduction ? Une idée qui fait son chemin
1. Dix ans plus tard
2. Un défi à relever
2.1 Analyse de la situation
2.1.1 Contexte économique de l'industrie de la chaussure au Canada
2.1.2 Un état des lieux de notre usine
2.2 La solution : le système de production Lean de Toyota et le kaizen
2.2.1 Par où commencer?
2.2.2 Notre façon de procéder
3. Repenser l'aménagement de l'usine et la philosophie de production
3.1 Le module, centre névralgique de la production
3.1.1 La conception et l'aménagement du module pilote
3.1.2 Le choix d'un module en U
3.2 L'organisation et la méthode de fabrication traditionnelles
3.3 L'expérimentation de nouvelles façons de faire
3.4 Une comparaison des résultats obtenus
3.5 La présentation du budget de dépenses à la direction
4. Impliquer les employés
4.1 Inquiétudes et résistances au sein du personnel
4.2 Garanties et engagements de la compagnie
5. Réaménager et former
5.1 La planification et la mise en oeuvre du réaménagement
5.2 Des programmes de formation sur mesure
5.2.1 Couturières
5.2.2 Tailleurs
5.2.3 Superviseurs
6. Revoir la structure salariale et le système de primes
6.1 Une situation complexe
6.2 Une simplification indispensable
6.3 La recherche d'un consensus
7. Organiser le travail
7.1 Travail individuel contre travail en équipe
7.2 Une composition réfléchie des équipes
7.3 Une autonomie à développer
7.4 Une usine sans inspecteurs, est-ce possible?
7.5 Une mise à l'épreuve
7.6 Problèmes de démarrage et frictions
7.6.1 Des problèmes de santé
7.6.2 Des tensions dans les équipes
7.6.3 Des frustrations relatives au retrait de privilèges
7.7 Une concession au profit de l'ambiance de travail
8. Surmonter les obstacles
8.1 Un coup de tonnerre
8.2 Un projet qui tombe à point
8.3 Une étude préliminaire pour mettre le doigt sur les problèmes
8.3.1 Un portrait de la population de l'usine
8.3.2 Une première investigation sur les problèmes de santé
8.3.3 Une seconde investigation sur les problèmes de bien-être psychologique et la communication
8.3.4 Un bilan et un plan d'action concret
8.4 Le facilitateur, un agent de changement positif
8.5 De superviseur à coach, un poste en mutation
8.5.1 Le contremaître, ce mal-aimé !
8.5.2 Le passage de superviseur à coach, une transition difficile
8.5.3 Le choix de nouveaux superviseurs qui ont l'étoffe de coachs
9. Établir un système de partage des gains pour stimuler la productivité
9.1 Un système de primes qui nuit à l'objectif
9.2 La nécessité d'un nouveau modèle de partage des gains
9.2.1 Un plan de partage basé sur la productivité
9.2.2 Un comité employeur/employés pour mettre le plan sur pied
9.2.3 Après deux ans, un bilan mitigé des gains partagés
9.3 Une rectification de tir
9.3.1 Une nouvelle formation au juste à temps pour amener les employés à s'engager
9.3.2 Une révision du plan de partage des gains de productivité
9.3.3 Des résultats spectaculaires, mais fragiles
9.4 Un bilan qui incite à la vigilance
10. Effectuer un premier bilan et cerner les erreurs de parcours
10.1 La longueur de la courbe d'apprentissage
10.2 L'effet des goulots d'étranglement
10.3 L'ampleur des ajustements requis en matière de technologies de l'information
10.4 La durée d'implantation du main à main
11. Mettre le kaizen en pratique dans l'usine
11.1 Exemples de petits projets kaizen
11.1.1 Ajout d'une bande autoagrippante de type Velcro sur les machines à coudre
11.1.2 Installation d'un sac de récupération de retailles
11.1.3 Conception de tables d'emballage fonctionnelles
11.1.4 Conception d'un contenant à talonnettes
11.1.5 Instauration d'un code de couleurs pour l'injection et le transport des bases
11.2 Exemple d'un projet kaizen moyen
11.2.1 Installation d'un système de levage de boîte
11.3 Exemple d'un grand projet kaizen
11.3.1 Automatisation des tâches de taillage et d'encollage des ganses
11.4 Exemple de l'application du kaizen dans la vie de tous les jours
12. Visite d'un fournisseur chinois : le choc de la réalité
12.1 Plus qu'une entreprise : une ville!
12.2 Des employées en résidence
12.3 Le royaume du muda
12.4 De la qualité, mais aux dépens de la productivité
12.5 Une dure prise de conscience
12.6 Une lutte inégale
13. La fin d'une époque
13.1 Une concurrence mondiale de plus en plus féroce
13.2 Une usine productive, mais sous-utilisée
13.3 Une mode en mutation
13.4 Un concours de circonstance
13.5 Un constat inéluctable
13.5.1 Une décision pénible
13.5.2 Un douloureux délai
13.5.3 L'annonce de la fermeture
13.5.4 Les dernières semaines
13.6 L'après-Contrecoeur : le Lean à l'œuvre
14. Des conditions gagnantes pour réussir un projet d'implantation du JAT et du Lean
14.1 Un engagement inconditionnel de la haute direction
14.2 Une attitude de franchise et d'ouverture envers les travailleurs
14.3 Un engagement inconditionnel de tous les employés
14.4 Le choix du main à main ou flux tendu : simplement incontournable
14.5 L'aspiration de devenir une entreprise de classe mondiale
15. Système de production Lean de Toyota, kaizen et autres concepts associés
15.1 Système de production de Toyota et Lean
15.1.1 Management de la qualité totale
15.1.2 Juste à temps, flux tiré, flux tendu et temps takt
15.1.3 Maintenance productive totale, taux de rendement global et jidoka
15.2 Kaizen
15.2.1 Les 5S
15.2.2 Standardisation
15.2.3 Élimination des mudas
15.2.4 Management visuel
15.2.5 Programme de suggestions
15.2.6 Règles pour le bon fonctionnement du gemba
15.3 Système de production Lean de Toyota et kaizen en bref
16. Tournée d'usines japonaises de classe mondiale
16.1 Toyoda Iron Works
16.2 Yamaha Motors
16.3 NGK Insulators, usine Chita
16.4 Togo Seisakusho
16.5 Taiho Kogyo
16.6 Toyota, usine Takaoka
17. Mythes et réalités au sujet de l'industrie et des travailleurs japonais
17.1 Une discipline exceptionnelle
17.2 Des emplois à vie
17.3 Une chaîne de montage que n'importe qui peut arrêter
17.4 Des rejets au compte-gouttes
18. Les déboires de Toyota
18.1 Un accident hautement médiatisé
18.2 Une montagne qui accouche d'une souris
18.3 Des leçons à tirer
18.4 Une confiance à rebâtir
19. Le retour au bercail de la production nord-américaine
19.1 La délocalisation, une panacée pour les entreprises des pays développés et les pays récepteurs?
19.2 Le prix de la délocalisation
19.3 Le retour du balancier
Annexe ? Plans de primes et de partage des gains en productivité
Glossaire
Bibliographie
Avant-propos
Remerciements
Introduction ? Une idée qui fait son chemin
1. Dix ans plus tard
2. Un défi à relever
2.1 Analyse de la situation
2.1.1 Contexte économique de l'industrie de la chaussure au Canada
2.1.2 Un état des lieux de notre usine
2.2 La solution : le système de production Lean de Toyota et le kaizen
2.2.1 Par où commencer?
2.2.2 Notre façon de procéder
3. Repenser l'aménagement de l'usine et la philosophie de production
3.1 Le module, centre névralgique de la production
3.1.1 La conception et l'aménagement du module pilote
3.1.2 Le choix d'un module en U
3.2 L'organisation et la méthode de fabrication traditionnelles
3.3 L'expérimentation de nouvelles façons de faire
3.4 Une comparaison des résultats obtenus
3.5 La présentation du budget de dépenses à la direction
4. Impliquer les employés
4.1 Inquiétudes et résistances au sein du personnel
4.2 Garanties et engagements de la compagnie
5. Réaménager et former
5.1 La planification et la mise en oeuvre du réaménagement
5.2 Des programmes de formation sur mesure
5.2.1 Couturières
5.2.2 Tailleurs
5.2.3 Superviseurs
6. Revoir la structure salariale et le système de primes
6.1 Une situation complexe
6.2 Une simplification indispensable
6.3 La recherche d'un consensus
7. Organiser le travail
7.1 Travail individuel contre travail en équipe
7.2 Une composition réfléchie des équipes
7.3 Une autonomie à développer
7.4 Une usine sans inspecteurs, est-ce possible?
7.5 Une mise à l'épreuve
7.6 Problèmes de démarrage et frictions
7.6.1 Des problèmes de santé
7.6.2 Des tensions dans les équipes
7.6.3 Des frustrations relatives au retrait de privilèges
7.7 Une concession au profit de l'ambiance de travail
8. Surmonter les obstacles
8.1 Un coup de tonnerre
8.2 Un projet qui tombe à point
8.3 Une étude préliminaire pour mettre le doigt sur les problèmes
8.3.1 Un portrait de la population de l'usine
8.3.2 Une première investigation sur les problèmes de santé
8.3.3 Une seconde investigation sur les problèmes de bien-être psychologique et la communication
8.3.4 Un bilan et un plan d'action concret
8.4 Le facilitateur, un agent de changement positif
8.5 De superviseur à coach, un poste en mutation
8.5.1 Le contremaître, ce mal-aimé !
8.5.2 Le passage de superviseur à coach, une transition difficile
8.5.3 Le choix de nouveaux superviseurs qui ont l'étoffe de coachs
9. Établir un système de partage des gains pour stimuler la productivité
9.1 Un système de primes qui nuit à l'objectif
9.2 La nécessité d'un nouveau modèle de partage des gains
9.2.1 Un plan de partage basé sur la productivité
9.2.2 Un comité employeur/employés pour mettre le plan sur pied
9.2.3 Après deux ans, un bilan mitigé des gains partagés
9.3 Une rectification de tir
9.3.1 Une nouvelle formation au juste à temps pour amener les employés à s'engager
9.3.2 Une révision du plan de partage des gains de productivité
9.3.3 Des résultats spectaculaires, mais fragiles
9.4 Un bilan qui incite à la vigilance
10. Effectuer un premier bilan et cerner les erreurs de parcours
10.1 La longueur de la courbe d'apprentissage
10.2 L'effet des goulots d'étranglement
10.3 L'ampleur des ajustements requis en matière de technologies de l'information
10.4 La durée d'implantation du main à main
11. Mettre le kaizen en pratique dans l'usine
11.1 Exemples de petits projets kaizen
11.1.1 Ajout d'une bande autoagrippante de type Velcro sur les machines à coudre
11.1.2 Installation d'un sac de récupération de retailles
11.1.3 Conception de tables d'emballage fonctionnelles
11.1.4 Conception d'un contenant à talonnettes
11.1.5 Instauration d'un code de couleurs pour l'injection et le transport des bases
11.2 Exemple d'un projet kaizen moyen
11.2.1 Installation d'un système de levage de boîte
11.3 Exemple d'un grand projet kaizen
11.3.1 Automatisation des tâches de taillage et d'encollage des ganses
11.4 Exemple de l'application du kaizen dans la vie de tous les jours
12. Visite d'un fournisseur chinois : le choc de la réalité
12.1 Plus qu'une entreprise : une ville!
12.2 Des employées en résidence
12.3 Le royaume du muda
12.4 De la qualité, mais aux dépens de la productivité
12.5 Une dure prise de conscience
12.6 Une lutte inégale
13. La fin d'une époque
13.1 Une concurrence mondiale de plus en plus féroce
13.2 Une usine productive, mais sous-utilisée
13.3 Une mode en mutation
13.4 Un concours de circonstance
13.5 Un constat inéluctable
13.5.1 Une décision pénible
13.5.2 Un douloureux délai
13.5.3 L'annonce de la fermeture
13.5.4 Les dernières semaines
13.6 L'après-Contrecoeur : le Lean à l'œuvre
14. Des conditions gagnantes pour réussir un projet d'implantation du JAT et du Lean
14.1 Un engagement inconditionnel de la haute direction
14.2 Une attitude de franchise et d'ouverture envers les travailleurs
14.3 Un engagement inconditionnel de tous les employés
14.4 Le choix du main à main ou flux tendu : simplement incontournable
14.5 L'aspiration de devenir une entreprise de classe mondiale
15. Système de production Lean de Toyota, kaizen et autres concepts associés
15.1 Système de production de Toyota et Lean
15.1.1 Management de la qualité totale
15.1.2 Juste à temps, flux tiré, flux tendu et temps takt
15.1.3 Maintenance productive totale, taux de rendement global et jidoka
15.2 Kaizen
15.2.1 Les 5S
15.2.2 Standardisation
15.2.3 Élimination des mudas
15.2.4 Management visuel
15.2.5 Programme de suggestions
15.2.6 Règles pour le bon fonctionnement du gemba
15.3 Système de production Lean de Toyota et kaizen en bref
16. Tournée d'usines japonaises de classe mondiale
16.1 Toyoda Iron Works
16.2 Yamaha Motors
16.3 NGK Insulators, usine Chita
16.4 Togo Seisakusho
16.5 Taiho Kogyo
16.6 Toyota, usine Takaoka
17. Mythes et réalités au sujet de l'industrie et des travailleurs japonais
17.1 Une discipline exceptionnelle
17.2 Des emplois à vie
17.3 Une chaîne de montage que n'importe qui peut arrêter
17.4 Des rejets au compte-gouttes
18. Les déboires de Toyota
18.1 Un accident hautement médiatisé
18.2 Une montagne qui accouche d'une souris
18.3 Des leçons à tirer
18.4 Une confiance à rebâtir
19. Le retour au bercail de la production nord-américaine
19.1 La délocalisation, une panacée pour les entreprises des pays développés et les pays récepteurs?
19.2 Le prix de la délocalisation
19.3 Le retour du balancier
Annexe ? Plans de primes et de partage des gains en productivité
Glossaire
Bibliographie
Gestionnaires et aux dirigeants d'entreprise, étudiants en gestion et en
génie industrie
Diplômé de Polytechnique Montréal en génie industriel, Joe Bichai est vice-président fabrication chez Genfoot (fabricant de la marque Kamik) depuis 25 ans.
Considéré comme un chef de file dans le monde de la production Lean et fervent partisan de la fabrication locale, il a prononcé de nombreuses conférences devant des pairs. Il a été invité à maintes reprises à partager avec des étudiants universitaires ses connaissances sur la philosophie Lean et l'amélioration continue (kaizen), secrets de la compétitivité sur l'échiquier mondial.
En 1998, la Société canadienne de génie industriel lui a décerné le prix de Leadership pour la promotion du génie industriel et de la productivité, et en 2000, il a reçu du Département de génie industriel de Polytechnique Montréal le prestigieux prix Rayonnement, remis à l'ingénieur le plus influent de sa décennie.
Considéré comme un chef de file dans le monde de la production Lean et fervent partisan de la fabrication locale, il a prononcé de nombreuses conférences devant des pairs. Il a été invité à maintes reprises à partager avec des étudiants universitaires ses connaissances sur la philosophie Lean et l'amélioration continue (kaizen), secrets de la compétitivité sur l'échiquier mondial.
En 1998, la Société canadienne de génie industriel lui a décerné le prix de Leadership pour la promotion du génie industriel et de la productivité, et en 2000, il a reçu du Département de génie industriel de Polytechnique Montréal le prestigieux prix Rayonnement, remis à l'ingénieur le plus influent de sa décennie.
Gagnant du prix or des projets présentés au Salon sur les meilleures pratiques d'affaires 2015
Date de parution : 02-2017
Ouvrage de 223 p.
16x23.5 cm
Thèmes d’Agir ou périr dans la jungle de la mondialisation :
© 2024 LAVOISIER S.A.S.