Piping and Instrumentation Diagram Development
Auteur : Toghraei Moe
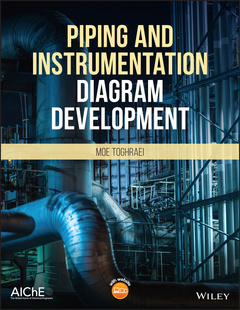
An essential guide for developing and interpreting piping and instrumentation drawings
Piping and Instrumentation Diagram Development is an important resource that offers the fundamental information needed for designers of process plants as well as a guide for other interested professionals. The author offers a proven, systemic approach to present the concepts of P&ID development which previously were deemed to be graspable only during practicing and not through training.
This comprehensive text offers the information needed in order to create P&ID for a variety of chemical industries such as: oil and gas industries; water and wastewater treatment industries; and food industries. The author outlines the basic development rules of piping and instrumentation diagram (P&ID) and describes in detail the three main components of a process plant: equipment and other process items, control system, and utility system. Each step of the way, the text explores the skills needed to excel at P&ID, includes a wealth of illustrative examples, and describes the most effective practices.
This vital resource:
- Offers a comprehensive resource that outlines a step-by-step guide for developing piping and instrumentation diagrams
- Includes helpful learning objectives and problem sets that are based on real-life examples
- Provides a wide range of original engineering flow drawing (P&ID) samples
- Includes PDF?s that contain notes explaining the reason for each piece on a P&ID and additional samples to help the reader create their own P&IDs
Written for chemical engineers, mechanical engineers and other technical practitioners, Piping and Instrumentation Diagram Development reveals the fundamental steps needed for creating accurate blueprints that are the key elements for the design, operation, and maintenance of process industries.
Preface xix
Acknowledgement xxiii
About the Companion Website xxv
Part I Fundamentals of P&ID Development 1
1 What Is P&ID 3
1.1 Why Is P&ID Important? 3
1.2 What Is a P&ID? 4
1.3 P&ID Media 4
1.4 P&ID Development Activity 5
2 Management of P&ID Development 9
2.1 Project of Developing P&IDs 9
2.2 P&ID Milestones 9
2.3 Involved Parties in P&ID Development 11
2.4 P&ID Set Owner 12
2.5 Required Quality of the P&ID in Each Stage of Development 12
2.6 P&ID Evolution 12
2.7 Tracking Changes in P&IDs 12
2.8 Required Man‐Hours for the Development of P&IDs 13
3 Anatomy of a P&ID Sheet 15
3.1 Title Block 15
3.2 Ownership Block 15
3.3 Reference Drawing Block 15
3.4 Revision Block 15
3.5 Comments Block 16
3.6 Main Body of a P&ID 19
4 General Rules in Drawing of P&IDs 21
4.1 Items on P&IDs 21
4.1.1 Pipes or Other Flow Conductors 21
4.1.2 Equipment 21
4.1.3 Instruments 21
4.1.4 Signals 22
4.2 How to Show Them: Visual Rules 22
4.2.1 Line Crossing Over 24
4.2.2 Equipment Crossing 25
4.2.3 Off‐Page Connector 26
4.2.4 Color in P&IDs 26
4.3 Item Identifiers in P&IDs 26
4.3.1 Symbols 27
4.3.2 Tags 28
4.3.3 Name 29
4.3.4 Technical Information 29
4.4 Different Types of P&IDs 32
4.4.1 Legend P&IDs 33
4.4.2 System P&IDs 34
4.4.3 Network P&IDs 34
4.4.4 Interarea P&IDs 34
4.4.5 Detail P&IDs 36
4.5 A Set of P&IDs 39
4.6 P&IDs Prepared in Engineering Companies Compared to Manufacturing or Fabricating Companies 42
4.7 Dealing with Vendor or Licensor P&IDs 43
5 Principles of P&ID Development 45
5.1 Plant Stakeholders 45
5.2 The Hierarchy of P&ID Development Rules 45
5.3 Plant Operations 46
5.3.1 Process Parameters 46
5.3.2 Process Parameter Levels 47
5.3.2.1 Pressure Levels 48
5.3.2.2 Temperature Levels 49
5.3.2.3 Liquid/Solid Levels 49
5.3.2.4 Flow Levels 50
5.3.2.5 Analyte Levels 50
5.3.3 Parameter Levels versus Control System 50
5.3.4 Parameter Levels versus Safety 51
5.3.5 Parameter Levels versus Operator Role 52
5.3.6 General Procedure of P&ID Development 53
5.4 What Should a P&ID Address? 53
5.4.1 Normal Operation 53
5.4.2 Nonroutine Operation 53
5.4.2.1 Reduced Capacity Operation 54
5.4.3 Reduced Efficiency Operation 57
5.4.4 Start‐Up Operations 58
5.4.5 Shutdown 59
5.4.6 Inspection and Maintenance 60
5.4.6.1 Quantitative Approach to Maintenance Requirement 60
5.4.6.2 Qualitative Approach to Maintenance Requirement 60
5.4.7 Operability in Absence of One Item 61
5.4.8 Provision for the Future 61
5.5 Conflicting Check and Merging Opportunities Check 63
5.5.1 Conflict Check 63
5.5.2 Merging Opportunities Check 63
5.6 Dealing with Common Challenges in P&ID Development 64
5.7 Example: Development of P&ID of a Typical Pump 65
Part II Pipes and Equipment 69
6 Pipes 71
6.1 Fluid Conductors: Pipes, Tubes, and Ducts 71
6.2 Pipe Identifiers 71
6.2.1 Pipe Symbol 71
6.2.2 Pipe Tag 71
6.2.2.1 Do All Pipes Need to be Tagged? 73
6.2.2.2 Which Span of Pipe Route can be Considered One Piece of Pipe? 73
6.2.2.3 How is the Pipe Tag Shown on a P&ID? 73
6.2.3 Pipe Off‐Page Connector 74
6.3 Pipe Tag Anatomy 74
6.3.1 Area or Project Number 74
6.3.2 Commodity Acronym 74
6.3.3 Pipe Material Specification Code 74
6.3.4 Pipe Size 77
6.3.5 Pipe Sequential Number 78
6.3.6 Other Pipe Tag Information 78
6.4 Pipes Crossing “Borders” 79
6.4.1 Implementing Spec Break 80
6.4.2 Reasons for a Spec Break 82
6.5 Goal of Piping 82
6.5.1 Magnitude of Flow in Pipe 83
6.5.2 Direction of Flow in Pipe 84
6.5.3 Providing Fluid with Enough Pressure at the Inlet 84
6.6 Piping Arrangements 84
6.6.1 Backflow Prevention Systems 85
6.6.2 Diversion of Flow 87
6.6.3 Distribution of Flow 87
6.7 Pipe Route 88
6.7.1 Slope 88
6.7.2 No Liquid Pocket 89
6.7.3 No Gas Pocket 89
6.7.4 Free Draining (Self‐Draining) 89
6.7.5 Free Venting 90
6.7.6 Gravity Flow 90
6.7.7 Vertical or Horizontal Pipe 90
6.7.8 Straight Piping 90
6.7.9 Minimum or Maximum Length or Distance 90
6.7.10 Other Special Pipe Routes 91
6.8 Piping Movement 91
6.9 Dealing with Unwanted Two‐Phase Flow in Pipes 92
6.9.1 Liquid–Gas Two‐Phase Flow 92
6.9.2 Gas–Liquid Two‐Phase Flow 94
6.9.3 Solid–Liquid Two‐Phase Flow 94
6.10 Tubes 94
6.11 Double–Wall Pipes 95
6.12 Pipes for Special Arrangements 96
6.12.1 Piping for Bypassing 96
6.12.2 Piping for Recirculation 96
6.12.3 Piping for Units in Series 96
6.12.4 Piping for Units in Parallel 97
6.12.5 Piping for Pressure Equalization 97
6.13 Pipe Size Rule of Thumbs 97
6.14 Pipe Appurtenances 97
6.14.1 Pipe Fittings 98
6.14.1.1 Pipe Direction Change 98
6.14.1.2 Reducers (Enlargers) 98
6.14.1.3 Three‐Way Connections 100
6.14.1.4 Pipe Connections 100
6.14.1.5 End‐of‐Pipe Systems 100
6.14.2 Specialty Items 102
6.14.2.1 Flange‐Insulating Gasket 102
6.15 Other Approach about Piping 103
6.16 “Merging” Pipes 103
6.17 Wrapping–Up: Addressing Requirements of Pipe during the Life Span 103
6.18 Transferring Bulk Solid Materials 104
Reference 104
7 Manual Valves and Automatic Valves 105
7.1 Valve Naming 105
7.2 Valve Functions 105
7.3 Valve Structure 105
7.4 Classification of Valves 105
7.4.1 Valve Plug: Throttling vs. Blocking Valves 106
7.4.2 Valve Selection 108
7.4.3 Multi‐port Valves 108
7.4.4 Double‐Seated Valves 110
7.5 Valve Operators 110
7.6 Different Types of Actuators 111
7.7 Basis of Operation for Automatic Valves 112
7.8 Tagging Automatic Valves 113
7.9 Tagging Manual Valves 113
7.10 Valve Positions 113
7.10.1 Regular Position of Blocking Valves and Decision Methodology 113
7.10.2 Failure Position of Automatic Valves and Decision Methodology 114
7.10.3 More Concepts about Failure Position of Automatic Valves 115
7.11 Valve Arrangement 117
7.11.1 Valves in Series 118
7.11.2 Valves in Parallel 118
7.12 Control Valves and RO Combinations 119
7.13 Operating in the Absence of Valves 119
7.13.1 Operating in the Absence of Control Valves 119
7.13.2 Operating in the Absence of Switching Valves 122
7.14 Valves in Role of Unit Operation 122
7.15 Special Valves 123
7.15.1 Check Valves 123
7.15.2 Regulators 124
7.15.3 Safety‐Related Valves 125
7.16 Valve Combinations 126
7.17 End of Valve Arrangements 126
7.18 Valve Sizing Rule of Thumbs 127
7.19 Merging Valves 127
7.20 Wrapping Up: Addressing Requirements of Valve During the Life Span 127
References 128
8 Provisions for Ease of Maintenance 129
8.1 Introduction 129
8.2 Different Types of Equipment Care 129
8.3 In‐place In‐line Equipment Care 129
8.4 In‐place Off‐line Equipment Care 130
8.5 In‐workshop Off‐line Equipment Care 131
8.6 Preparing Equipment for Off‐line Care 131
8.7 Isolation 131
8.7.1 Requirement of an Isolation System 131
8.7.2 Type of Isolation System 132
8.7.3 Placement of an Isolation System 135
8.7.4 Inbound Versus Outbound Blind Location 135
8.7.5 Merging Isolation Valves 135
8.8 Bringing the Equipment to a Non‐harmful Condition 136
8.8.1 Cooling Down 136
8.8.2 Emptying and Then Draining/Venting 136
8.8.2.1 Location and Number of Drain/Vent Valves 137
8.8.2.2 Size of Drain/Vent Valves 138
8.8.2.3 Other Usages of Drain/Vent Valves 138
8.9 Cleaning 139
8.9.1 Solid/Semi‐Solid Removal Methods 139
8.9.2 Washing Systems 139
8.9.3 Purging Methods 140
8.10 Ultimate Destination of Dirty Fluids 140
8.11 Making Equipment Easy to Remove 141
8.12 Wrap‐up 142
9 Containers 143
9.1 Introduction 143
9.2 Selection of Containers 143
9.3 Containers Purposes 144
9.4 Transferring Fluids Between Containers 145
9.5 Container Positions 146
9.6 Container Shapes 147
9.6.1 Closing Parts of Containers 148
9.6.2 Open Top or Fully Enclosed Containers 148
9.7 Container Identifiers 148
9.7.1 Container Symbol 148
9.7.2 Container Tags 149
9.7.3 Container Call‐outs 149
9.7.3.1 Tank Call‐outs 149
9.7.3.2 Vessel Call‐outs 150
9.7.3.3 Tag of Container in Duty of Conversion 151
9.8 Levels in Non‐flooded Liquid Containers 151
9.9 Container Nozzles 151
9.9.1 Nozzle Duties 151
9.9.2 Nozzle Locations 152
9.9.3 Nozzle Elevation Versus Liquid Levels 153
9.9.4 The Size, Number, and Rating of Nozzles 155
9.9.5 Merging Nozzles 155
9.9.6 Nozzle Internal Assemblies 156
9.9.7 Nozzle Externals 157
9.10 Overflow Nozzles 157
9.11 Breathing of Non‐flooded Containers 158
9.12 Blanketed Tanks 160
9.13 Heating (or Cooling) in Containers 161
9.14 Mixing in Containers 162
9.15 Container Internals 162
9.16 Tank Roofs 162
9.17 Tank Floors 163
9.18 Container Arrangement 164
9.19 Merging Containers 164
9.20 Secondary Containment 165
9.21 Underground Storage Tanks 166
9.22 Sumps 167
9.23 Wrapping‐up: Addressing the Requirements of the Container During its Lifespan 167
10 Pumps and Compressors 169
10.1 Introduction 169
10.2 Fluid Mover Roles 169
10.3 Types of Fluid Movers 169
10.4 A Brief Discussion on the Function of Fluid Movers in a System 169
10.5 Fluid Mover Identifiers 171
10.5.1 Fluid Mover Symbol 171
10.5.2 Fluid Mover Tag 171
10.5.3 Fluid Mover Call‐out 173
10.6 Liquid Movers: Dynamic Pumps 173
10.6.1 Centrifugal Pumps 173
10.6.1.1 P&ID Development on the Suction Side 174
10.6.1.2 P&ID Development on the Discharge Side 175
10.6.2 Low Flow Intolerance and Minimum Flow Protection System 176
10.6.2.1 Which Pumps May Need a Minimum Flow Pipe 176
10.6.2.2 Where Should we Position the Recirculation Line? 177
10.6.2.3 Where Should the Destination Point of the Recirculation Pipe Be? 177
10.6.2.4 What Should the Size of the Recirculation Pipe Be? 178
10.6.2.5 What Should the Arrangement on the Recirculation Pipe Be? 178
10.6.3 Cavitation 180
10.6.4 Very Small Centrifugal Pumps 181
10.6.5 Different Types of Spare Pump 182
10.6.6 Centrifugal Pump Arrangements 182
10.6.6.1 Centrifugal Pumps in Parallel 183
10.6.6.2 Centrifugal Pumps in Series 184
10.6.7 Pump Warm‐up or Cool‐down System 185
10.6.8 Piping Spec. for Centrifugal Pumps 187
10.6.9 Centrifugal Pump Drives 187
10.6.10 (Liquid) Seal Systems in Centrifugal Pumps 187
10.6.11 Merging Pumps 189
10.7 Liquid Movers: PD Pumps 190
10.7.1 PD Pump P&ID Piping 191
10.7.1.1 Reciprocating Pumps P&ID Piping 191
10.7.1.2 Rotary Pumps P&ID Piping 192
10.7.2 PD Pump Arrangements 193
10.7.3 Merging PD Pumps 193
10.7.4 Tying Together Dissimilar Pumps 193
10.7.5 PD Pump Drives 193
10.7.6 Sealing Systems for PD Pumps 194
10.7.7 Metering Pumps (Dosing Pumps) 194
10.7.8 Liquid Transfer – Summary 195
10.7.9 Pumps: Duty Other than Pumping! 195
10.8 Gas Movers: Fans, Blowers, Compressors 196
10.8.1 Low Flow Intolerance and Anti‐Surge Systems 196
10.8.2 P&ID Development of Gas Movers 197
10.8.3 Gas Mover Drives 198
10.8.4 Auxiliary Systems Around Fluid Movers 198
10.8.5 Gas Transfer – Summary 199
10.9 Wrapping‐up: Addressing Requirements of Fluid Movers During the Life Span 200
Reference 200
11 Heat Transfer Units 201
11.1 Introduction 201
11.2 Main Types of Heat Transfer Units 201
11.3 Different Types of Heat Exchangers and Their Selection 202
11.4 Different Types of Heat Transfer Fluids and Their Selection 203
11.5 Heat Exchangers: General Naming 204
11.6 Heat Exchanger Identifiers 204
11.6.1 Heat Exchanger Symbol 204
11.6.2 Heat Exchanger Tag 204
11.6.3 Heat Exchanger Call‐Out 205
11.7 Heat Exchanger P&ID 206
11.7.1 Vents and Drains 206
11.7.2 Isolation Valves 207
11.7.3 Chemical Cleaning Valves 207
11.7.4 PSDs 207
11.8 Heat Exchanger Arrangement 207
11.8.1 Heat Exchangers in Series 207
11.8.2 Heat Exchangers in Parallel 209
11.9 Aerial Coolers 209
11.9.1 Aerial Cooler P&ID 210
11.9.2 Dealing with Extreme Temperatures 211
11.9.3 Aerial Cooler Arrangement 211
11.10 Merging Heat Exchangers 212
11.11 Wrapping‐up: Addressing the Requirements of a Heat Exchanger During its Life Span 212
11.12 Fired Heaters and Furnaces 213
11.12.1 Process Fluid Side 213
11.12.2 Flue Gas Side 213
11.12.3 Firing Side 214
11.13 Fire Heater Arrangement 215
11.14 Merging Fired Heaters 216
11.15 Wrapping‐up: Addressing the Requirements of Fired Heaters During their Lifespan 216
12 Pressure Relief Devices 217
12.1 Introduction 217
12.2 Why Pressure Is So Important? 217
12.3 Dealing with Abnormal Pressures 217
12.3.1 Active Versus Passive Solutions 219
12.3.2 Where Could Passive Solutions Be Used? 219
12.3.3 Where Should Active Solutions Be Used? 219
12.4 Safety Relief System 219
12.5 What Is an “Enclosure,” and Which “Side” Should Be Protected? 220
12.6 Regulatory Issues Involved in PRVs 220
12.6.1 Codes Versus Standards 221
12.7 PRD Structure 222
12.8 Six Steps to Providing a Protective Layer 222
12.9 Locating PRDs 223
12.10 Positioning PRDs 223
12.11 Specifying the PRD 225
12.12 Selecting the Right Type of PRD 225
12.12.1 Pressure Relief Valve Type 225
12.12.2 Rupture Disks 226
12.12.3 Decision General Rules 226
12.13 PRD Identifiers 226
12.13.1 PRD Symbols and Tags 226
12.13.2 PRD Technical Information 227
12.14 Selecting the Right Type of PRD Arrangement 228
12.15 Deciding on an Emergency Release Collecting Network 230
12.16 Deciding on a Disposal System 232
12.16.1 Liquid Disposal 232
12.16.2 Gas/Vapor Disposal 233
12.16.3 Two‐Phase Flow Handling 234
12.17 Protecting Atmospheric Containers 235
12.18 Merging PRDs 236
12.19 Wrapping‐Up: Addressing the Requirements of PRDs During their Lifespan 238
Part III Instrumentation and Control System 239
13 Fundamentals of Instrumentation and Control 241
13.1 What Is Process Control? 241
13.2 Components of Process Control Against Violating Parameters 241
13.3 Parameters Versus Steering/Protecting Components 242
13.4 How Many Steering Loops Are Needed? 242
13.5 ICSS System Technology 243
13.5.1 Use of PLC for a BPCS 243
13.5.2 Use of DCS for a SIS 244
13.5.3 Alarm Systems 244
13.5.4 ICSS System Symbology 244
13.6 ICSS Elements 245
13.7 Basic Process Control System (BPCS) 245
13.8 Instruments on P&IDs 247
13.8.1 Fundamental Terminology 247
13.8.2 Identifiers for Equipment and Instrumentation 247
13.9 Instrument Identifiers 248
13.9.1 Acronyms 248
13.9.2 Divider Types 249
13.9.3 Symbol Type 250
13.9.4 Additional Information and Tag Number 252
13.10 Signals: Communication Between Instruments 252
13.10.1 Signal Types 253
13.10.2 Signal Functions 253
13.10.3 Signal Math Functions 254
13.10.4 Signal Selectors 254
13.11 Different Instrument Elements 255
13.11.1 Primary Instruments 255
13.11.1.1 Temperature Measurement 256
13.11.1.2 Pressure Measurement 257
13.11.1.3 Level Measurement 258
13.11.1.4 Flow Measurement 258
13.11.1.5 Process Analyzers 260
13.11.2 Transmitters 262
13.11.3 Controllers 263
13.11.4 Indicators 263
13.11.5 Final Control Elements in a BPCS 263
13.11.5.1 Control Valves 264
13.11.5.2 Variable Speed Devices on Electric Motors 264
13.12 Simple Control Loops 264
13.12.1 Level Control Loops 265
13.12.2 Pressure Control Loops 265
13.12.3 Temperature Control Loops 265
13.12.4 Composition Control Loops 266
13.12.5 Flow Control Loops 266
13.13 Position of Sensor Regarding Control Valves 266
14 Application of Control Architectures 269
14.1 Introduction 269
14.2 Control System Design 269
14.3 Selecting the Parameter to Control 269
14.4 Identifying the Manipulated Stream 270
14.5 Determining the Set Point 271
14.6 Building a Control Loop 272
14.6.1 Feedback Versus Feedforward 272
14.6.2 Single‐ versus Multiple‐Loop Control 273
14.7 Multi‐Loop Control Architectures 274
14.7.1 Cascade Control 274
14.8 Feedforward Plus Feedback Control 276
14.8.1 Ratio or Relationship Control 279
14.8.2 Selective Control 280
14.8.3 Override and Limit Control 281
14.8.3.1 Override Control 283
14.8.3.2 Limit Control 286
14.8.4 Split Range and Parallel Control 286
14.8.5 Clarification of Confusion 288
14.8.5.1 Cascade Versus Ratio 288
14.8.5.2 Single Loop Versus Ratio 288
14.8.5.3 Selective Versus Override 288
14.9 Monitoring Parameters 289
14.9.1 Container Sensors 290
14.9.2 Fluid Mover Sensors 290
14.9.3 Heat Exchanger Sensors 291
14.9.4 Fired Heater Sensors 291
15 Plant Process Control 293
15.1 Introduction 293
15.2 Plant‐Wide Control 293
15.3 Heat and Mass Balance Control 293
15.4 Surge Control 295
15.4.1 Disturbances in Process Parameters 295
15.4.2 Disturbance Management 296
15.4.2.1 Absorption 296
15.4.2.2 Rejection 296
15.4.3 Disturbance Versus Fluid Phase 296
15.4.4 Dampening Gas/Vapor Flow Surge 297
15.4.5 Dampening Liquid Flow Surge 298
15.4.6 The Purpose of Containers in Process Plants 301
15.5 Equipment Control 302
15.5.1 Do We Need to Control at All? 302
15.5.2 Principles of Equipment‐wise Control 302
15.6 Pipe Control System 304
15.6.1 Control of a Single Pipe 304
15.6.1.1 Control of Pressure in a Pipe 304
15.6.1.2 Control of Flow in a Pipe 304
15.6.2 Controlling Multiple Pipes 306
15.6.2.1 Flow Merging 306
15.6.2.2 Flow Splitting 308
15.7 Fluid Mover Control System 309
15.7.1 Pump Control Systems 310
15.7.1.1 Centrifugal Pump Control 310
15.7.1.2 Positive Displacement (PD) Pump 314
15.7.2 Gas Mover Control Systems 316
15.7.2.1 Capacity Control Methods for Gas Movers 316
15.7.3 Anti‐Surge Control 319
15.7.4 Lead–Lag Operation of Fluid‐Movers 319
15.8 Heat Transfer Equipment Control 320
15.8.1 Heat Exchanger Control System 320
15.8.1.1 Direct Control System 320
15.8.1.2 Bypass Control System 321
15.8.1.3 Control of Heat Exchangers Experiencing Phase Change 324
15.8.2 Air Cooler Control 327
15.8.3 Heat Exchanger for Heat Recovery 327
15.8.4 Back Pressure Control of Heat Exchangers 328
15.8.5 Fired Heater Control 328
15.9 Container Control System 331
15.10 Blanket Gas Control Systems 332
Reference 332
16 Plant Interlocks and Alarms 333
16.1 Introduction 333
16.2 Safety Strategies 333
16.3 Concept of a SIS 333
16.4 SIS Actions and SIS Types 333
16.5 SIS Extent 336
16.6 Deciding on the Required SIS 336
16.7 The Anatomy of a SIS 336
16.7.1 SIS Element Symbols 336
16.7.1.1 SIS Primary Elements: Sensors 337
16.7.2 SIS Final Elements 337
16.7.2.1 Switching Valves 337
16.7.2.2 Switching Valve Actuator Arrangements 338
16.7.2.3 Valve Position Validation 338
16.7.2.4 Merging a Switching Valve and a Control Valve 338
16.7.2.5 On/off Action of Electric Motors 339
16.7.3 SIS Logic 339
16.8 Showing Safety Instrumented Functions on P&IDs 340
16.9 Discrete Control 343
16.10 Alarm System 344
16.10.1 Anatomy of Alarm Systems 345
16.10.2 Alarm Requirements 345
16.10.3 Alarm System Symbology 346
16.10.4 Concept of “Common Alarm” 347
16.11 Fire and Gas Detection System (FGS) 347
16.11.1 Manual Alarm 350
16.12 Electric Motor Control 351
16.12.1 Simple Motor Control 351
16.12.2 The Focal Element of Motor Control: mcc 351
16.12.3 All About Relationships with Electric Motors 351
16.12.4 P&ID Representation of Commands and Responses 352
16.12.5 P&ID Representation of Principal Arrangement for Inspection and Repair 353
16.12.6 Examples 355
Part IV Utilities 357
17 Utilities 359
17.1 Utility System Components 359
17.2 Developing P&IDs for Utility Systems 359
17.2.1 Identifying the Utility Users 359
17.2.2 Utility Distribution and Collection Network Topologies 359
17.2.3 Designing the Detail of a Utility Network 361
17.2.4 Placing Priority on Utility Users 362
17.2.5 Connection Details of Utility to Process 363
17.3 Different Utilities in Plants 363
17.4 Air as a Utility in Process Plants 363
17.4.1 Instrument Air (IA) 363
17.4.2 Utility Air (UA) or Plant Air (PA) 364
17.5 Water as a Utility in Process Plants 364
17.5.1 Utility Water (UW) or Plant Water (PW) 364
17.5.2 Potable Water 364
17.6 Heat Transfer Media 364
17.6.1 Steam 365
17.7 Condensate Collection Network 366
17.8 Fuel as Utility 366
17.8.1 Fuel Oil 366
17.8.2 Fuel Gas 366
17.9 Inert Gas 367
17.9.1 Blanket Gas 367
17.9.2 Purging Gas 367
17.10 Vapor Collection Network 367
17.11 Emergency Vapor/Gas Release Collection Network 368
17.12 Fire Water 368
17.13 Surface Drainage Collection Network or Sewer System 370
17.14 Utility Circuits 372
17.14.1 Air Circuit 372
17.14.2 Steam–Condensate Circuit 374
17.14.3 Cooling Water Circuit 375
17.14.4 Natural Gas Preparation System 375
17.15 Connection Between Distribution and Collecting Networks 375
Part V Additional Information and General Procedure 379
18 Ancillary Systems and Additional Considerations 381
18.1 Introduction 381
18.2 Safety Issues 381
18.2.1 Different Types of Hazards 381
18.2.2 Hazards and Injuries 381
18.2.3 Mechanical Hazards 381
18.2.4 Chemical Hazards 382
18.2.5 Energy Hazards 382
18.2.5.1 Noise Barrier 382
18.2.5.2 Burning Prevention 382
18.2.6 Safety Showers and Eye Washers 383
18.3 Dealing with Environment 384
18.3.1 Arrangements for Maintaining the Temperature of the Process 384
18.3.2 Winterization 385
18.3.3 Deciding on the Extent of Insulation 389
18.3.4 Summary of Insulation 390
18.4 Utility Stations 390
18.5 Off‐Line Monitoring Programs 392
18.5.1 The Program Component 392
18.5.2 Sampling System 393
18.5.3 Sample Extraction Device 393
18.5.4 Sample Transferring Tube 394
18.5.5 Sample Conditioning System 394
18.5.6 Sample Hand‐Over System 395
18.5.7 Waste Sample Collection System 395
18.5.8 Sampling Station Structural Frame 395
18.5.9 Showing a Sampling System on P&IDs 396
18.5.10 Sampling System for Process Analyzers 396
18.6 Corrosion Monitoring Program 396
18.7 Impact of the Plant Model on the P&ID 397
18.8 Design Pressure and Temperature Considerations 398
18.8.1 Decision on “Design Pressure @ Design Temperature” Pair 399
18.8.1.1 Deciding on “Design Pressure” 399
18.8.1.2 Deciding on “Design Temperature” 399
18.8.2 Sources of Rebel Pressures 400
18.8.3 Sources of Rebel Temperatures 400
18.8.4 Design Pressure and Design Temperature of Single Process Elements 400
18.8.5 Design Pressure of Connected Items 401
18.8.5.1 Design Pressure of Connected Equipment–Equipment 402
18.8.5.2 Design Pressure of Connected Equipment–Sensor 403
19 General Procedures 405
19.1 Introduction 405
19.2 General Procedure for P&ID Development 405
19.2.1 P&ID Development: Piping and Equipment 405
19.2.2 P&ID Development: Control and Instruments 406
19.3 P&ID Reviewing and Checking 409
19.3.1 Format Check 409
19.3.2 Demonstration Rules Check 410
19.3.3 Technical Check 410
19.3.4 Design Check 412
19.4 Methods of P&ID Reviewing and Checking 412
19.4.1 Systematic Approach 412
19.4.2 Scanning Approach 412
19.5 Required Quality of P&IDs at Each Stage of Development 413
20 Examples 417
Index 453
MOE TOGHRAEI is an independent consultant and instructor. He has more than 20 years of experience in the chemical process industries. He provides consultancy in process and project engineering areas. He also has developed and instructed dozens of technical courses, including tailor-made courses for companies, public courses and online courses. His online courses are available through the University of Kansas and University of Dalhousie.
Date de parution : 04-2019
Ouvrage de 496 p.
21.4x27.4 cm
Thème de Piping and Instrumentation Diagram Development :
Mots-clés :
Guide to Piping and Instrumentation Diagram Development; Understanding Piping and Instrumentation Diagram Development; resource to Piping and Instrumentation Diagram Development; nature of piping and instrumentation; importance of piping and instrumentation; developing of piping and instrumentation; equipment for piping and instrumentation; piping instrumentation control system; pipe appurtenances; pipe valves manual and automatic; containers tanks and vessels; fluid movers pumps compressors fans blowers; heat exchangers; inspection and maintenance; pressure safety devices; integrated control and safety in piping; developing control loops on piping and instrumentation design; utility systems in process plant; tracing insulation "utility stations"