Machine Design (6th Ed.) An Integrated Approach
Auteur : Norton Robert
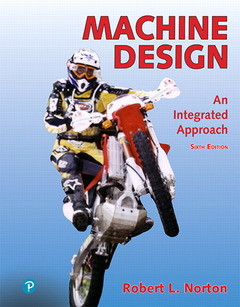
For courses in Machine Design.
An integrated, case-based approach to machine design
Machine Design: An Integrated Approach, 6th Edition presents machine design in an up-to-date and thorough manner with an emphasis on design. Author Robert Norton draws on his 50-plus years of experience in mechanical engineering design, both in industry and as a consultant, as well as 40 of those years as a university instructor in mechanical engineering design.
Written at a level aimed at junior-senior mechanical engineering students, the textbook emphasizes failure theory and analysis as well as the synthesis and design aspects of machine elements. Independent of any particular computer program, the book points out the commonality of the analytical approaches needed to design a wide variety of elements and emphasizes the use of computer-aided engineering as an approach to the design and analysis of these classes of problems.
Also available with Mastering Engineering
Mastering? is the teaching and learning platform that empowers you to reach every student. By combining trusted author content with digital tools developed to engage students and emulate the office-hour experience, Mastering personalizes learning and often improves results for each student. Tutorial exercises and author-created tutorial videos walk students through how to solve a problem, consistent with the author?s voice and approach from the book.
Note: You are purchasing a standalone product; Mastering Engineering does not come packaged with this content. Students, if interested in purchasing this title with Mastering Engineering, ask your instructor for the correct package ISBN and Course ID. Instructors, contact your Pearson representative for more information.
If you would like to purchase both the physical text and Mastering Engineering, search for:
0136606539/9780136606536 Machine Design: An Integrated Approach Plus MasteringEngineering with Pearson eText -- Access Card Package 6/e
Package consists of:
- 0135166802/9780135166802 MasteringEngineering with Pearson eText -- Access Card -- for Machine Design: An Integrated Approach, 6/e
- 0135184231 / 9780135184233 Machine Design: An Integrated Approach, 6/e
Brief Contents
PART I: FUNDAMENTALS
- Introduction to Design
- 1.1 Design
- Machine Design
- 1.2 A Design Process
- 1.3 Problem Formulation and Calculation
- Definition Stage
- Preliminary Design Stage
- Detailed Design Stage
- Documentation Stage
- 1.4 The Engineering Model
- Estimation and First-Order Analysis
- The Engineering Sketch
- 1.5 Computer-Aided Design and Engineering
- Computer-Aided Design (CAD)
- Computer-Aided Engineering (CAE)
- Computational Accuracy
- 1.6 The Engineering Report
- 1.7 Factors of Safety and Design Codes
- Factor of Safety
- Choosing a Safety Factor
- Design and Safety Codes
- 1.8 Statistical Considerations
- 1.9 Units
- 1.10 Summary
- 1.11 References
- 1.12 Web References
- 1.13 Bibliography
- 1.14 Problems
- 1.1 Design
- Materials and Processes
- 2.0 Introduction
- 2.1 Material-Property Definitions
- The Tensile Test
- Ductility and Brittleness
- The Compression Test
- The Bending Test
- The Torsion Test
- Fatigue Strength and Endurance Limit
- Impact Resistance
- Fracture Toughness
- Creep and Temperature Effects
- 2.2 The Statistical Nature of Material Properties
- 2.3 Homogeneity and Isotropy
- 2.4 Hardness
- Heat Treatment
- Surface (Case) Hardening
- Heat Treating Nonferrous Materials
- Mechanical Forming and Hardening
- 2.5 Coatings and Surface Treatments
- Galvanic Action
- Electroplating
- Electroless Plating
- Anodizing
- Plasma-Sprayed Coatings
- Chemical Coatings
- 2.6 General Properties of Metals
- Cast Iron
- Cast Steels
- Wrought Steels
- Steel Numbering Systems
- Aluminum
- Titanium
- Magnesium
- Copper Alloys
- 2.7 General Properties of Nonmetals
- Polymers
- Ceramics
- Composites
- 2.8 Selecting Materials
- 2.9 Summary
- 2.10 References
- 2.11 Web References
- 2.12 Bibliography
- 2.13 Problems
- Kinematics and Load Determination
- 3.0 Introduction
- 3.1 Degree of Freedom
- 3.2 Mechanisms
- 3.3 Calculating Degree of Freedom (Mobility)
- 3.4 Common 1-DOF Mechanisms
- Fourbar Linkage and the Grashof Condition
- Sixbar Linkage
- Cam and Follower
- 3.5 Analyzing Linkage Motion
- Types of Motion
- Complex Numbers as Vectors
- The Vector Loop Equation
- 3.6 Analyzing the Fourbar Linkage
- Solving for Position in the Fourbar Linkage
- Solving for Velocity in the Fourbar Linkage
- Angular Velocity Ratio and Mechanical Advantage
- Solving for Acceleration in the Fourbar Linkage
- 3.7 Analyzing the Fourbar Crank-Slider
- Solving for Position in the Fourbar Crank-Slider
- Solving for Velocity in the Fourbar Crank-Slider
- Solving for Acceleration in the Fourbar Crank-Slider
- Other Linkages
- 3.8 Cam Design and Analysis
- The Timing Diagram
- The svaj Diagram
- Polynomials for the Double-Dwell Case
- Polynomials for the Single-Dwell Case
- Pressure Angle
- Radius of Curvature
- 3.9 Loading Classes For Force Analysis
- 3.10 Free-body Diagrams
- 3.11 Load Analysis
- Three-Dimensional Analysis
- Two-Dimensional Analysis
- Static Load Analysis
- 3.12 Two-Dimensional, Static Loading Case Studies
- 3.13 Three-Dimensional, Static Loading Case Study
- 3.14 Dynamic Loading Case Study
- 3.15 Vibration Loading
- Natural Frequency
- Dynamic Forces
- 3.16 Impact Loading
- Energy Method
- 3.17 Beam Loading
- Shear and Moment
- Singularity Functions
- Superposition
- 3.18 Summary
- 3.19 References
- 3.20 Web References
- 3.21 Bibliography
- 3.22 Problems
- Stress, Strain, and Deflection
- 4.0 Introduction
- 4.1 Stress
- 4.2 Strain
- 4.3 Principal Stresses
- 4.4 Plane Stress and Plane Strain
- Plane Stress
- Plane Strain
- 4.5 Mohr’s Circles
- 4.6 Applied Versus Principal Stresses
- 4.7 Axial Tension
- 4.8 Direct Shear Stress, Bearing Stress, and Tearout
- Direct Shear
- Direct Bearing
- Tearout Failure
- 4.9 Beams and Bending Stresses
- Beams in Pure Bending
- Shear Due to Transverse Loading
- 4.10 Deflection in Beams
- Deflection by Singularity Functions
- Statically Indeterminate Beams
- 4.11 Castigliano’s Method
- Deflection by Castigliano’s Method
- Finding Redundant Reactions with Castigliano’s Method
- 4.12 Torsion
- 4.13 Combined Stresses
- 4.14 Spring Rates
- 4.15 Stress Concentration Stress Concentration Under Static Loading
- Stress Concentration Under Dynamic Loading
- Determining Geometric Stress-Concentration Factors
- Designing to Avoid Stress Concentrations
- 4.16 Axial Compression - Columns
- Slenderness Ratio
- Short Columns
- Long Columns
- End Conditions
- Intermediate Columns
- 4.17 Stresses in Cylinders
- Thick-Walled Cylinders
- Thin-Walled Cylinders
- 4.18 Case Studies in Static Stress and Deflection Analysis
- 4.19 Summary
- 4.20 References
- 4.21 Bibliography
- 4.22 Problems
- Static Failure Theories
- 5.0 Introduction
- 5.1 Failure of Ductile Materials Under Static Loading
- The von Mises-Hencky or Distortion-Energy Theory
- The Maximum Shear-Stress Theory
- The Maximum Normal-Stress Theory
- Comparison of Experimental Data with Failure Theories
- 5.2 Failure of Brittle Materials Under Static Loading
- Even and Uneven Materials
- The Coulomb-Mohr Theory
- The Modified-Mohr Theory
- 5.3 Fracture Mechanics
- Fracture-Mechanics Theory
- Fracture Toughness Kc
- 5.4 Using The Static Loading Failure Theories
- 5.5 Case Studies in Static Failure Analysis
- 5.6 Summary
- 5.7 References
- 5.8 Bibliography
- 5.9 Problems
- Fatigue Failure Theories
- 6.0 Introduction
- History of Fatigue Failure
- 6.1 Mechanism of Fatigue Failure
- Crack Initiation Stage
- Crack Propagation Stage
- Fracture
- 6.2 Fatigue-Failure Models
- Fatigue Regimes
- The Stress-Life Approach 3
- The Strain-Life Approach
- The LEFM Approach
- 6.3 Machine-Design Considerations
- 6.4 Fatigue Loads
- Rotating Machinery Loading
- Service Equipment Loading
- 6.5 Measuring Fatigue Failure Criteria
- Fully Reversed Stresses
- Combined Mean and Alternating Stress
- Fracture-Mechanics Criteria
- Testing Actual Assemblies
- 6.6 Estimating Fatigue Failure Criteria
- Estimating the Theoretical Fatigue Strength Sf ’ or Endurance Limit Se’
- Correction Factors—Theoretical Fatigue Strength or Endurance Limit
- Corrected Fatigue Strength Sf or Corrected Endurance Limit Se
- Creating Estimated S-N Diagrams
- 6.7 Notches and Stress Concentrations
- Notch Sensitivity
- 6.8 Residual Stresses
- 6.9 Designing for High-Cycle Fatigue
- 6.10 Designing for Fully Reversed Uniaxial Stresses
- Design Steps for Fully Reversed Stresses with Uniaxial Loading
- 6.11 Designing for Fluctuating Uniaxial Stresses
- Creating the Modified-Goodman Diagram
- Applying Stress-Concentration Effects with Fluctuating Stresses
- Determining the Safety Factor with Fluctuating Stresses
- Design Steps for Fluctuating Stresses
- 6.12 Designing for Multiaxial Stresses in Fatigue
- Frequency and Phase Relationships
- Fully Reversed Simple Multiaxial Stresses
- Fluctuating Simple Multiaxial Stresses
- Complex Multiaxial Stresses
- 6.13 A General Approach to High-Cycle Fatigue Design
- 6.14 A Case Study in Fatigue Design
- 6.15 Summary
- 6.16 References
- 6.17 Bibliography
- 6.18 Problems
- 6.0 Introduction
- Surface Failure
- 7.0 Introduction
- 7.1 Surface Geometry
- 7.2 Mating Surfaces
- 7.3 Friction
- Effect of Roughness on Friction
- Effect of Velocity on Friction
- Rolling Friction
- Effect of Lubricant on Friction
- 7.4 Adhesive Wear
- The Adhesive-Wear Coefficient
- 7.5 Abrasive Wear
- Abrasive Materials
- Abrasion-Resistant Materials
- 7.6 Corrosion Wear
- Corrosion Fatigue
- Fretting Corrosion
- 7.7 Surface Fatigue
- 7.8 Spherical Contact
- Contact Pressure and Contact Patch in Spherical Contact
- Static Stress Distributions in Spherical Contact
- 7.9 Cylindrical Contact
- Contact Pressure and Contact Patch in Parallel Cylindrical Contact
- Static Stress Distributions in Parallel Cylindrical Contact
- 7.10 General Contact
- Contact Pressure and Contact Patch in General Contact
- Stress Distributions in General Contact
- 7.11 Dynamic Contact Stresses
- Effect of a Sliding Component on Contact Stresses
- 7.12 Surface Fatigue Failure Models—Dynamic Contact
- 7.13 Surface Fatigue Strength
- 7.14 Summary
- 7.15 References
- 7.16 Problems
- Finite Element Analysis
- 8.0 Introduction
- Stress and Strain Computation
- 8.1 Finite Element Method
- 8.2 Element Types
- Element Dimension and Degree of Freedom (DOF)
- Element Order
- H-Elements Versus P-Elements
- Element Aspect Ratio
- 8.3 Meshing
- Mesh Density
- Mesh Refinement
- Convergence
- 8.4 Boundary Conditions
- 8.5 Applying Loads
- 8.6 Testing the Model (Verification)
- 8.7 Modal Analysis
- 8.8 Case Studies
- 8.9 Summary
- 8.10 References
- 8.11 Bibliography
- 8.12 Web Resources
- 8.13 Problems
- 8.0 Introduction
PART II: MACHINE DESIGN
- Design Case Studies
- 9.0 Introduction
- 9.1 Case Study 8—A Portable Air Compressor
- 9.2 Case Study 9—A Hay-Bale Lifter
- 9.3 Case Study 10—A Cam-Testing Machine
- 9.4 Summary
- 9.5 References
- 9.6 Design Projects
- Shafts, Keys, and Couplings
- 10.0 Introduction
- 10.1 Shaft Loads
- 10.2 Attachments and Stress Concentrations
- 10.3 Shaft Materials
- 10.4 Shaft Power
- 10.5 Shaft Loads
- 10.6 Shaft Stresses
- 10.7 Shaft Failure in Combined Loading
- 10.8 Shaft Design
- General Considerations
- Design for Fully Reversed Bending and Steady Torsion
- Design for Fluctuating Bending and Fluctuating Torsion
- 10.9 Shaft Deflection
- Shafts as Beams
- Shafts as Torsion Bars
- 10.10 Keys and Keyways
- Parallel Keys
- Tapered Keys
- Woodruff Keys
- Stresses in Keys
- Key Materials
- Key Design
- Stress Concentrations in Keyways
- 10.11 Splines
- 10.12 Interference Fits
- Stresses in Interference Fits
- Stress Concentration in Interference Fits
- Fretting Corrosion
- 10.13 Flywheel Design
- Energy Variation in a Rotating System
- Determining the Flywheel Inertia
- Stresses in Flywheels
- Failure Criteria
- 10.14 Critical Speeds of Shafts
- Lateral Vibration of Shafts and Beams—Rayleigh’s Method
- Shaft Whirl
- Torsional Vibration
- Two Disks on a Common Shaft
- Multiple Disks on a Common Shaft
- Controlling Torsional Vibrations
- 10.15 Couplings
- Rigid Couplings
- Compliant Couplings
- 10.16 Case Study 8B
- Designing Driveshafts for a Portable Air Compressor
- 10.17 Summary
- 10.18 References
- 10.19 Problems
- Bearings and Lubrication
- 11.0 Introduction
- A Caveat
- 11.1 Lubricants
- 11.2 Viscosity
- 11.3 Types of Lubrication
- Full-Film Lubrication
- Boundary Lubrication
- 11.4 Material Combinations in Sliding Bearings
- 11.5 Hydrodynamic Lubrication Theory
- Petroff’s Equation for No-Load Torque
- Reynolds’ Equation for Eccentric Journal Bearings
- Torque and Power Losses in Journal Bearings
- 11.6 Design of Hydrodynamic Bearings
- Design Load Factor—The Ocvirk Number
- Design Procedures
- 11.7 Nonconforming Contacts
- 11.8 Rolling-element Bearings
- Comparison of Rolling and Sliding Bearings
- Types of Rolling-Element Bearings
- 11.9 Failure of Rolling-element bearings
- 11.10 S election of Rolling-element bearings
- Basic Dynamic Load Rating C
- Modified Bearing Life Rating
- Basic Static Load Rating C0
- Combined Radial and Thrust Loads
- Calculation Procedures
- 11.11 Bearing Mounting Details
- 11.12 Special Bearings
- 11.13 Case Study 10B
- 11.14 Summary
- Important Equations Used in This Chapter
- 11.15 References
- 11.16 Problems
- 11.0 Introduction
- Spur Gears
- 12.0 Introduction
- 12.1 Gear Tooth Theory
- The Fundamental Law of Gearing
- The Involute Tooth Form
- Pressure Angle
- Gear Mesh Geometry
- Rack and Pinion
- Changing Center Distance
- Backlash
- Relative Tooth Motion
- 12.2 Gear Tooth Nomenclature
- 12.3 Interference and Undercutting
- Unequal-Addendum Tooth Forms
- 12.4 Contact Ratio
- 12.5 Gear Trains
- Simple Gear Trains
- Compound Gear Trains
- Reverted Compound Trains
- Epicyclic or Planetary Gear Trains
- 12.6 Gear Manufacturing
- Forming Gear Teeth
- Machining
- Roughing Processes
- Finishing Processes
- Gear Quality
- 12.7 Loading on Spur Gears
- 12.8 Stresses in Spur Gears
- Bending Stresses
- Surface Stresses
- 12.9 Gear Materials
- Material Strengths
- Bending-Fatigue Strengths for Gear Materials
- Surface-Fatigue Strengths for Gear Materials
- 12.10 Lubrication of Gearing
- 12.11 Design of Spur Gears
- 12.12 Case Study 8C
- 12.13 Summary
- 12.14 References
- 12.15 Problems
- Helical, Bevel, and Worm Gears
- 13.0 Introduction
- 13.1 Helical Gears
- Helical Gear Geometry
- Helical-Gear Forces
- Virtual Number of Teeth
- Contact Ratios
- Stresses in Helical Gears
- 13.2 Bevel Gears
- Bevel-Gear Geometry and Nomenclature
- Bevel-Gear Mounting
- Forces on Bevel Gears
- Stresses in Bevel Gears
- 13.3 Wormsets
- Materials for Wormsets
- Lubrication in Wormsets
- Forces in Wormsets
- Wormset Geometry
- Rating Methods
- A Design Procedure for Wormsets
- 13.4 Case Study 9B
- 13.5 Summary
- 13.6 References
- 13.7 Problems
- Spring Design
- 14.0 Introduction
- 14.1 Spring Rate
- 14.2 Spring Configurations
- 14.3 Spring Materials
- Spring Wire
- Flat Spring Stock
- 14.4 Helical Compression Springs
- Spring Lengths
- End Details
- Active Coils
- Spring Index
- Spring Deflection
- Spring Rate
- Stresses in Helical Compression Spring Coils
- Helical Coil Springs of Nonround Wire
- Residual Stresses
- Buckling of Compression Springs
- Compression-Spring Surge
- Allowable Strengths for Compression Springs
- The Torsional-Shear S-N Diagram for Spring Wire
- The Modified-Goodman Diagram for Spring Wire
- 14.5 Designing Helical Compression Springs for Static Loading
- 14.6 Designing Helical Compression Springs for Fatigue Loading
- 14.7 Helical Extension Springs
- Active Coils in Extension Springs
- Spring Rate of Extension Springs
- Spring Index of Extension Springs
- Coil Preload in Extension Springs
- Deflection of Extension Springs
- Coil Stresses in Extension Springs
- End Stresses in Extension Springs
- Surging in Extension Springs
- Material Strengths for Extension Springs
- Design of Helical Extension Springs
- 14.8 Helical Torsion Springs
- Terminology for Torsion Springs
- Number of Coils in Torsion Springs
- Deflection of Torsion Springs
- Spring Rate of Torsion Springs
- Coil Closure
- Coil Stresses in Torsion Springs
- Material Parameters for Torsion Springs
- Safety Factors for Torsion Springs
- Designing Helical Torsion Springs
- 14.9 Belleville Spring Washers
- Load-Deflection Function for Belleville Washers
- Stresses in Belleville Washers
- Static Loading of Belleville Washers
- Dynamic Loading
- Stacking Springs
- Designing Belleville Springs
- 14.10 Case Study 10C
- 14.11 Summary
- 14.12 References
- 14.13 Problems
- Screws and Fasteners
- 15.0 Introduction
- 15.1 Standard Thread Forms
- Tensile Stress Area
- Standard Thread Dimensions
- 15.2 Power Screws
- Square, Acme, and Buttress Threads
- Power Screw Application
- Power Screw Force and Torque Analysis
- Friction Coefficients
- Self-Locking and Back-Driving of Power Screws
- Screw Efficiency
- Ball Screws
- 15.3 Stresses in Threads
- Axial Stress
- Shear Stress
- Torsional Stress
- 15.4 Types of Screw Fasteners
- Classification by Intended Use
- Classification by Thread Type
- Classification by Head Style
- Nuts and Washers
- 15.5 Manufacturing Fasteners
- 15.6 Strengths of Standard Bolts and Machine Screws
- 15.7 Preloaded Fasteners in Tension
- Preloaded Bolts Under Static Loading
- Preloaded Bolts Under Dynamic Loading
- 15.8 Determining the Joint Stiffness Factor
- Joints With Two Plates of the Same Material
- Joints With Two Plates of Different Materials
- Gasketed Joints
- 15.9 Controlling Preload
- The Turn-of-the-Nut Method
- Torque-Limited Fasteners
- Load-Indicating Washers
- Torsional Stress Due to Torquing of Bolts
- 15.10 Fasteners in Shear
- Dowel Pins
- Centroids of Fastener Groups
- Determining Shear Loads on Fasteners
- 15.11 Case Study 8D
- 15.12 Summary
- 15.13 References
- 15.14 Bibliography
- 15.15 Problems
- Weldments
- 16.0 Introduction
- 16.1 Welding Processes
- Types of Welding in Common Use
- Why Should a Designer Be Concerned with the Welding Process?
- 16.2 Weld Joints and Weld Types
- Joint Preparation
- Weld Specification
- 16.3 Principles of Weldment Design
- 16.4 Static Loading of Welds
- 16.5 Static Strength of Welds
- Residual Stresses in Welds
- Direction of Loading
- Allowable Shear Stress for Statically Loaded Fillet and PJP Welds
- 16.6 Dynamic Loading of Welds
- Effect of Mean Stress on Weldment Fatigue Strength
- Are Correction Factors Needed For Weldment Fatigue Strength?
- Effect of Weldment Configuration on Fatigue Strength
- Is There an Endurance Limit for Weldments?
- Fatigue Failure in Compression Loading?
- 16.7 Treating a Weld as a Line
- 16.8 Eccentrically Loaded Weld Patterns
- 16.9 Design Considerations for Weldments in Machines
- 16.10 Summary
- 16.11 References
- 16.12 Problems
- Clutches and Brakes
- 17.0 Introduction
- 17.1 Types of Brakes and Clutches
- 17.2 Clutch/Brake Selection and Specification
- 17.3 Clutch and Brake Material
- 17.4 Disk Clutches
- Uniform Pressure
- Uniform Wear
- 17.5 Disk Brakes
- 17.6 Drum Brakes
- Short-Shoe External Drum Brakes
- Long-Shoe External Drum Brakes
- Long-Shoe Internal Drum Brakes
- 17.7 Summary
- 17.8 References
- 17.9 Bibliography
- 17.10 Problems
Appendices
- Material Properties
- Beam Tables
- Stress-Concentration Factors
- Answers to Selected Problems
Hallmark features of this title
- An integrated, case-based approach ties topics together via case studies, versus a string of disparate topics.
- A total of 967 problems sets are provided, with the majority designed to be independent within a chapter and the remaining sets designed to build upon succeeding chapters.
- Methods and techniques that take full advantage of computer-aided analysis are presented.
- The text is independent of any computer program.
- Computer files for the solution of all the examples and case studies written in several different languages (Mathcad, MATLAB, Excel, and TK Solver) are available for download.
- Several other programs written by the author are also provided as executable files.
Date de parution : 04-2020
Ouvrage de 1120 p.
10x10 cm