Bioceramic Coatings for Medical Implants Trends and Techniques
Auteurs : Heimann Robert B., Lehmann Hans D.
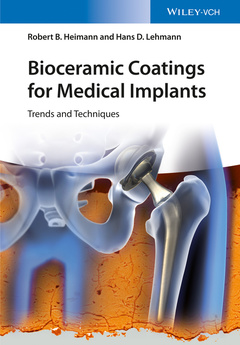
Following an introduction to the principles of biocompatibility, they present the structures and properties of various bioceramics from alumina to zirconia. The main part of the work focuses on coating technologies, such as chemical vapor deposition, sol-gel deposition and thermal spraying. There then follows a discussion of the major interactions of bioceramics with bone or tissue cells, complemented by an overview of the in-vitro testing methods of the biomineralization properties of bioceramics. The text is rounded off by chapters on the functionalization of bioceramic coatings and a look at future trends.
As a result, the authors bring together all aspects of the latest techniques for designing, depositing, testing, and implementing improved and novel bioceramic coating compositions, providing a full yet concise overview for beginners and professionals.
Preface XI
Glossary XVII
1 Bioceramics – A Historical Perspective 1
1.1 Alumina 1
1.2 Zirconia 3
1.3 Calcium Phosphates 4
References 6
2 Socio-Economic Aspects and Scope of Bioceramic Materials and Biomedical Implants 11
2.1 Types of Biomaterial 11
2.2 The Growing Global and Regional Markets for Biomedical Implants 14
2.2.1 A Worldwide Need for Implants 14
2.2.2 Market Projections and Forecasts for Biomaterials and Biomedical Implants 17
2.2.2.1 Biomaterials 17
2.2.2.2 Large-Joint Reconstructive Implants (Hip and Knee) 19
2.2.2.3 Small Joints and Extremities Implants 20
2.2.2.4 Spinal Implants 21
2.2.2.5 Dental Implants 21
2.3 Role of Bioceramic Coatings in Arthroplasty 22
2.4 Ceramic Femoral Ball Heads 26
2.4.1 Mechanical and Functional Properties 26
2.4.2 Manufacturing of Ceramic Femoral Ball Heads 27
2.4.3 Discolouration of Zirconia by Ionising Radiation 30
References 35
3 Fundamentals of Interaction of Bioceramics and Living Matter 41
3.1 Principle of Biocompatibility 41
3.2 Hierarchical Structure of Bone and Teeth 44
3.2.1 Bone Structure 44
3.2.2 Tooth Structure 47
3.3 Bioceramic/Bone Interface 49
3.3.1 Elasticity Mismatch 49
3.3.2 Interfacial Loosening 50
3.4 Basic Aspects of Biomineralisation 52
3.5 Interaction at a Cellular Level 53
3.6 Interaction at a Tissue Level 55
3.7 Advantages of Hydroxyapatite and Bioglass Coatings 60
3.8 The Promise of Cytokines 62
References 64
4 Structure and Properties of Bioceramics Used in Orthopaedic and Dental Implants 69
4.1 Bioinert Ceramics 69
4.1.1 Alumina 69
4.1.2 Stabilised Zirconia 74
4.1.2.1 Transformation Toughening of Zirconia Ceramics 75
4.1.2.2 Mechanical Properties of Zirconia 81
4.1.2.3 Biocompatibility and Hydrolytic Stability of Zirconia 81
4.2 Bioactive Ceramics 83
4.2.1 Surface-Active Bioglasses 84
4.2.2 Hydroxyapatite 89
4.2.3 Transition Metal-Substituted Calcium Orthophosphates 95
4.2.4 Resorbable Calcium Orthophosphates 98
4.2.4.1 Tricalcium Phosphates 99
4.2.4.2 Tetracalcium Phosphate 102
4.2.4.3 Ca–PO4 Sheet Structures 103
4.2.4.4 Highly Soluble Alkali-Containing Calcium Orthophosphates 103
4.2.4.5 Other Resorbable Bioceramics 104
References 105
5 Technology of Coating Deposition 113
5.1 Overview 113
5.2 Non-Thermal Deposition Methods 115
5.2.1 Biomimetic Route 115
5.2.1.1 General Aspects 115
5.2.1.2 Chemistry of Biomimetic Precipitation 117
5.2.1.3 Biomimetic Calcium Phosphate Coatings Deposited on Various Substrates 123
5.2.2 Sol–Gel Deposition 132
5.2.2.1 Titania Films and Coatings 133
5.2.2.2 Hydroxyapatite 135
5.2.2.3 Other Types of Coating 141
5.2.3 Dip and Spin Coating 143
5.2.3.1 Dip Coating 143
5.2.3.2 Spin Coating 145
5.2.4 Electrochemical Deposition (ECD) 146
5.2.4.1 Electrochemical Reactions 147
5.2.4.2 Acid–Base Reactions 147
5.2.4.3 Precipitation Reactions 148
5.2.5 Electrophoretic Deposition (EPD) 152
5.2.5.1 General Aspects 152
5.2.5.2 Electrophoretic Deposition of Calcium Phosphate Coatings 154
5.2.6 Thermal Substrate Deposition (Hydroprocessing) 158
5.2.7 Hydrothermal Coating Deposition 162
5.2.8 Electron- and Ion Beam-Assisted Deposition (EBAD, IBAD) 163
5.2.9 Radio Frequency (r.f.) Magnetron Sputtering 167
5.3 Thermal Deposition Methods 172
5.3.1 Atmospheric Plasma Spraying (APS) 173
5.3.1.1 The Physics Behind the Process 173
5.3.1.2 Micro-Plasma Spraying (MPS) and Low Energy Plasma Spraying (LEPS) 179
5.3.2 Low-Pressure (Vacuum) Plasma Spraying (LPPS, VPS) 182
5.3.3 Suspension Plasma Spraying (SPS) 185
5.3.3.1 Hydroxyapatite Coatings 188
5.3.3.2 Titanium Oxide Coatings 190
5.3.3.3 Bioglass Coatings 191
5.3.3.4 Other Types of Coating 192
5.3.4 High Velocity Suspension Flame Spraying (HVSFS) 193
5.3.4.1 Hydroxyapatite Coatings 194
5.3.4.2 Titanium Oxide Coatings 196
5.3.4.3 Bioglass Coatings 197
5.3.4.4 Other Coatings 199
5.3.5 Solution Precursor Plasma Spraying (SPPS) 200
5.3.6 Cold Gas Dynamic Spraying (CGDS) 201
5.3.6.1 Fundamentals 201
5.3.6.2 Bioceramic Coatings 204
5.3.7 Plasma Electrolytic Oxidation (PEO) 209
5.3.7.1 Magnesium Substrates 212
5.3.7.2 Titanium Substrates 214
5.3.8 Pulsed Laser Deposition (PLD) 219
5.4 Other Techniques 222
5.4.1 Flame Spraying 222
5.4.1.1 Oxygen/Acetylene Flame Spraying 222
5.4.1.2 High Velocity Oxyfuel Spraying (HVOF) 222
5.4.2 Inductively Coupled Plasma Spraying (ICPS) 224
5.4.3 Chemical Vapour Deposition (CVD) 224
5.4.4 Laser Alloying 226
5.4.5 Phase Inversion Technique 226
References 227
6 Deposition, Structure, Properties and Biological Function of Plasma-Sprayed Bioceramic Coatings 253
6.1 General Requirements and Performance Profile of Plasma-Sprayed Bioceramic Coatings 253
6.2 Structure and Biomedical Functions of Bioceramic Coatings 258
6.2.1 Hydroxyapatite Coatings 258
6.2.1.1 Microstructural and Compositional Changes During Plasma Spraying and Incubation in SBF 258
6.2.1.2 Thermal Decomposition of Hydroxyapatite During Plasma Spraying 263
6.2.1.3 Parametric Study of Thermal Decomposition of Hydroxyapatite 269
6.2.1.4 The Oxyapatite Problem 272
6.2.1.5 Biological Responses to Hydroxyapatite Coatings 275
6.2.2 Composite Coatings 278
6.2.2.1 Hydroxyapatite/Titania Composite Coatings 278
6.2.2.2 Hydroxyapatite/Zirconia Composite Coatings 278
6.2.2.3 Hydroxyapatite/Alumina/Carbon Nanotube Composite Coatings 280
6.2.3 Biphasic Hydroxyapatite/Tricalcium Phosphate Coatings 280
6.2.4 Transition Metal-Substituted Calcium Orthophosphate Coatings 281
6.2.4.1 Coating Thickness 281
6.2.4.2 Coating Porosity 282
6.2.4.3 Tensile Adhesion and Shear Strengths 283
6.3 The Role of Bond Coats 283
6.3.1 Engineering the Substrate–Coating Interface 283
6.3.2 Selected Bond Coats 285
6.3.2.1 Calcium Silicate Bond Coats 285
6.3.2.2 Titania Bond Coats 288
6.3.2.3 Zirconia Bond Coats 292
6.3.2.4 Mixed Zirconia/Titania Bond Coats 294
References 298
7 Characterisation and Testing of Bioceramic Coatings 309
7.1 Phase Composition: X-ray Diffraction 310
7.1.1 Fundamentals 310
7.1.2 X-ray Diffraction of Plasma-Sprayed Hydroxyapatite Coatings 312
7.2 Phase Composition: Vibrational (Infrared and Raman) Spectroscopy 314
7.2.1 Fundamentals 314
7.2.1.1 Infrared Spectroscopy 314
7.2.1.2 Raman Spectroscopy 315
7.2.2 Raman Microscopy of Bioceramic and Photoactive Titania Coatings 316
7.2.3 Infrared and Raman Spectra of Hydroxyapatite Coatings 318
7.2.3.1 Fourier Transform Infrared (FTIR) Spectroscopy 318
7.2.3.2 Raman spectroscopy 321
7.3 Phase Composition: Nuclear Magnetic Resonance Spectroscopy 325
7.3.1 Fundamentals 325
7.3.2 NMR Spectra of Hydroxyapatite Coatings 326
7.4 Phase Composition: Cathodoluminescence 333
7.4.1 Fundamentals 333
7.4.2 Cathodoluminescence Microscopy of Plasma-Sprayed Hydroxyapatite Coatings 334
7.5 Adhesion of Coatings to the Substrate 340
7.5.1 Fundamentals 340
7.5.1.1 Tensile Pull Test 342
7.5.1.2 Modified Peel Test 343
7.5.1.3 Scratch Testing 346
7.5.1.4 Ultrasonic Testing 349
7.5.2 Adhesion of Plasma-Sprayed Hydroxyapatite Coatings 351
7.5.2.1 Modified Peel Test According to ASTM D3167-10 351
7.5.2.2 Tensile Test 353
7.5.2.3 Scratch Test 354
7.5.2.4 Laser Shock Adhesion Test (LASAT) 356
7.6 Residual Coating Stresses 358
7.6.1 Fundamentals 358
7.6.2 X-ray Diffraction Measurements (sin2Ψ-Technique) 361
7.6.3 Stress Determination by Curvature Measurement (Almen-Type Test) 363
7.6.4 Hole-Drilling Strain Gauge Method 365
7.6.5 Photoluminescence Piezospectroscopy 367
7.6.6 Residual Stresses in Plasma-Sprayed Hydroxyapatite Coatings 370
7.6.6.1 Stress Analysis by X-ray Diffraction 370
7.6.6.2 Stress Analysis by Curvature Measurement 374
7.6.6.3 Stress Analysis by the Hole-Drilling Strain Gauge Method 376
7.6.6.4 Stress Analysis by Raman Piezospectroscopy 377
7.7 Fundamentals of Roughness and Porosity 377
7.8 Microhardness 382
7.8.1 Fundamentals 382
7.8.2 Microhardness of Hydroxyapatite Coatings 386
7.9 Potentiodynamic Polarisation and Electrochemical Impedance Spectroscopy (EIS) 387
7.9.1 Fundamentals 387
7.9.2 Corrosion Protection of Metal Implants through Coatings 389
7.10 Biological Performance Testing of Bioceramic Coatings 392
7.10.1 Composition of Simulated Body Fluids 393
7.10.2 Interaction of Simulated Body Fluids and Coatings 394
7.10.2.1 Structure and Transformation of Amorphous Calcium Phosphate (ACP) 395
7.10.2.2 EELS and PIXE Studies 402
7.10.3 Cell Proliferation and Viability Tests 405
7.10.3.1 Alkaline Phosphatase (ALP) Activity 405
7.10.3.2 Expression of Non-collagenous Proteins 406
7.10.3.3 AlamarBlue® and MTT Assays 409
7.10.3.4 Fluorescence Staining 411
7.10.4 In vivo Testing of Bioceramic Coatings Using Animal Models 414
7.10.4.1 Rat Model 416
7.10.4.2 Rabbit Model 417
7.10.4.3 Dog Model 420
7.10.4.4 Sheep Model 423
7.10.4.5 Other Animal Models 429
References 429
8 Future Developments and Outlook 445
References 451
Appendix: Relevant Scientific Journals/Book Series with Bioceramic Content 455
Index 459
Hans D. Lehmann is an organic chemist with an extensive working experience in polymer chemistry and polymer processing technology. He received his Diploma in chemistry from the Martin Luther University Halle-Wittenberg, Germany, in 1962. He worked as a polymer chemist and team leader in production-related research at the chemical company VEB BUNA (now Dow Chemical and Styron Deutschland, respectively). He specialized in the development of polymerization catalysts, modeling of monomer and polymer syntheses as well as their processing technologies and analytics. Moreover, until Germany?s reunification Hans Dieter Lehmann was responsible for the coordination between academia, industry and government. Since 1994 he worked as a consultant for patent law and process concepts, and co-authored several patents related to structural and functional surface coatings
Date de parution : 05-2015
Ouvrage de 496 p.
17.5x25.2 cm