Process Plant Equipment Operation, Control, and Reliability
Coordonnateurs : Holloway Michael D., Nwaoha Chikezie, Onyewuenyi Oliver A.
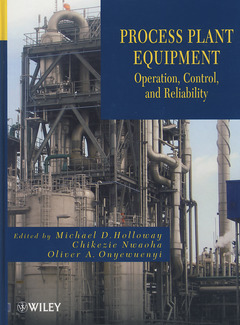
?Process Plant Equipment Book is another great publication from Wiley as a reference book for final year students as well as those who will work or are working in chemical production plants and refinery?? -Associate Prof. Dr. Ramli Mat, Deputy Dean (Academic), Faculty of Chemical Engineering, Universiti Teknologi Malaysia
??give[s] readers access to both fundamental information on process plant equipment and to practical ideas, best practices and experiences of highly successful engineers from around the world? The book is illustrated throughout with numerous black & white photos and diagrams and also contains case studies demonstrating how actual process plants have implemented the tools and techniques discussed in the book. An extensive list of references enables readers to explore each individual topic in greater depth?? ?Stainless Steel World and Valve World, November 2012
Discover how to optimize process plant equipment, from selection to operation to troubleshooting
From energy to pharmaceuticals to food, the world depends on processing plants to manufacture the products that enable people to survive and flourish. With this book as their guide, readers have the information and practical guidelines needed to select, operate, maintain, control, and troubleshoot process plant equipment so that it is efficient, cost-effective, and reliable throughout its lifetime. Following the authors' careful explanations and instructions, readers will find that they are better able to reduce downtime and unscheduled shutdowns, streamline operations, and maximize the service life of processing equipment.
Process Plant Equipment: Operation, Control, and Reliability is divided into three sections:
- Section One: Process Equipment Operations covers such key equipment as valves, pumps, cooling towers, conveyors, and storage tanks
- Section Two: Process Plant Reliability sets forth a variety of tested and proven tools and methods to assess and ensure the reliability and mechanical integrity of process equipment, including failure analysis, Fitness-for-Service assessment, engineering economics for chemical processes, and process component function and performance criteria
- Section Three: Process Measurement, Control, and Modeling examines flow meters, process control, and process modeling and simulation
Throughout the book, numerous photos and diagrams illustrate the operation and control of key process equipment. There are also case studies demonstrating how actual process plants have implemented the tools and techniques discussed in the book. At the end of each chapter, an extensive list of references enables readers to explore each individual topic in greater depth.
In summary, this text offers students, process engineers, and plant managers the expertise and technical support needed to streamline and optimize the operation of process plant equipment, from its initial selection to operations to troubleshooting.
Contributors xxiii
Preface xxiv
SECTION I PROCESS EQUIPMENT OPERATION
1 Introduction 3
Michael D. Holloway
2 Valves 9
Ali Ahammad Shoukat Choudhury, Chikezie Nwaoha, and Sharad Vishwasrao
2.1 Types of Control Valves, 10
2.2 Control Valve Actuators, 12
2.3 Control Valve Sizing and Selection, 13
2.4 Common Problems of Control Valves, 15
2.5 Diagnosing Control Valve Problems, 19
2.6 Control Valve Reliability and Selection, 20
2.7 Control Valve Maintenance, 22
2.8 Control Valve Troubleshooting, 24
References, 24
3 Pumps 27
Craig Redmond
3.1 Types of Pumps, 28
3.2 Pump Applications, 34
3.3 Pump Sizing and Selection, 37
3.4 Pump Maintenance, 40
3.5 Pump Troubleshooting, 44
4 Pipes 45
Shaohui Jia
4.1 Types of Pipes, 45
4.2 Pipe Selection, 46
4.3 Pipeline Network Design and Optimization, 48
4.4 Pipeline Failure, 50
4.5 Pipeline Inspection and Leak Detection, 54
4.6 Pipe Maintenance, 58
4.7 Pipe Troubleshooting, 60
References, 61
5 Cooling Towers 63
Zaki Yamani Zakaria and Chikezie Nwaoha
5.1 Cooling Tower Operation, 63
5.2 Types of Cooling Towers, 69
5.3 Common Problems of Cooling Towers, 74
5.4 Measuring Cooling Tower Performance, 75
5.5 Cooling Tower Maintenance, 77
References, 79
6 Filters and Membranes 81
Flora Tong and Chikezie Nwaoha
6.1 Types of Filters, 81
6.2 Mechanisms of Filtration, 87
6.3 Filter Selection, 87
6.4 Particle-Size Measurement Techniques, 88
6.5 Filter Location, 89
6.6 Membrane Filtration, 89
6.7 Filter Maintenance, 103
References, 104
7 Sealing Devices 107
Matt Tones and Jim Drago
7.1 Gaskets, 107
7.2 Compression Packings, 125
7.3 Mechanical Seals, 131
7.4 Expansion Joints, 147
7.5 General Sealing Device Selection, 157
References, 161
8 Steam Traps 163
Jacob E. Uche and Chikezie Nwaoha
8.1 Steam Trap Operation, 163
8.2 Types of Steam Traps, 164
8.3 Steam Trap Installation, 172
8.4 Steam Trap Checking, 172
8.5 Common Problems of Steam Traps, 175
8.6 Steam Trap Selection, 176
8.7 Steam Trap Applications, 178
8.8 Steam Trap Sizing, 178
8.9 Steam Trap Maintenance, 181
References, 181
9 Process Compressors 183
N. Sitaram and Chikezie Nwaoha
9.1 Types of Compressors, 183
9.2 Continuous Compression Compressors, 184
9.3 Intermittent Compression Compressors, 186
9.4 Centrifugal Compressors, 189
9.5 Reciprocating Piston Compressors, 202
9.6 Compressor Troubleshooting, 209
References, 210
Further Reading, 211
10 Conveyors 213
Okenna Obi-Njoku
10.1 Industrial Use of Conveyors, 213
10.2 Types of Conveyors, 214
10.3 Conveyor Selection, 221
10.4 Conveyor Safety, 221
10.5 Conveyor Maintenance, 222
10.6 Summary, 222
References, 223
11 Storage Tanks 225
Marcello Ferrara and Chikezie Nwaoha
11.1 Types of Storage Tanks, 225
11.2 Storage Tank Classification, 227
11.3 Construction Materials, 227
11.4 Common Problems of Storage Tanks, 229
11.5 Storage Tank Maintenance, 233
11.6 Tank Appurtenances, 241
11.7 Storage Tank Maintenance, 243
References, 244
12 Mixers 245
Jayesh Ramesh Tekchandaney
12.1 Mixing Concepts: Theory and Practice, 246
12.2 Fluid Mixing, 248
12.3 Solid Blending, 264
12.4 Mixing High-Viscosity Materials and Pastes, 274
12.5 Mechanical Components in Mixing Equipment, 284
References, 295
13 Boilers 297
Celestine C. G. Nwankwo
13.1 Types of Boilers, 298
13.2 Boiler Accessories, 303
13.3 Boiler Selection, 305
13.4 Common Problems of Boilers, 306
13.5 Boiler Failure Analysis and Welding Defects, 308
13.6 Boiler Maintenance, 313
13.7 Boiler Troubleshooting, 319
13.8 Boiler Chemicals, 321
13.9 Boiler Efficiency and Combustion, 325
References, 327
Further Reading, 328
SECTION II PROCESS PLANT RELIABILITY
14 Engineering Economics for Chemical Processes 331
Alberto R. Betancourt-Torcat, L. A. Ricardez-Sandoval, and Ali Elkamel
14.1 Time Value of Money, 331
14.2 Cash Flow Analysis, 333
14.3 Profitability Analysis, 336
14.4 Cost Estimation and Project Evaluation, 340
References, 353
15 Process Component Function and Performance Criteria 355
Robert Free
15.1 Material Classification, 355
15.2 General Physical Quantities and Considerations, 356
15.3 Material Transfer and Conveyance Equipment, 366
15.4 Conveyors, 367
15.5 Pumps, 394
15.6 Valves, 400
15.7 Pipes, 405
15.8 Conclusions, 410
References, 410
Corporation Web Sites, 411
16 Failure Analysis and Interpretation of Components 413
Michael D. Holloway
16.1 Assessing the Situation, 413
16.2 Failure Defined, 414
16.3 Taking Advantage of Failure, 415
16.4 Sources of Failure, 416
16.5 Failure of Materials and of Machines, 416
16.6 Types of Forces, 417
16.7 Strength, 418
16.8 Creep (Deformation), 419
16.9 Fatigue (Material), 420
16.10 Wear, 422
16.11 Property Changes, 423
16.12 Temperature, 423
16.13 Oxidation: Molecular Transitions and Chemical Influences, 425
16.14 Deposit Formation, 426
16.15 Factors that Affect Deposit Formation, 428
16.16 Documenting Failure, 429
References, 432
17 Mechanical Integrity of Process Vessels and Piping 435
Oliver A. Onyewuenyi
17.1 Perspectives on Mechanical Integrity, Fitness for Service, and Condition Monitoring, 437
17.2 Types of Flaws and Damage Mechanisms, 439
17.3 Inspection, Characterization, and Monitoring of Flaws, 442
17.4 Fracture Mechanics and Fitness-for-Service Assessment, 443
17.5 Control and Prevention of Brittle Fracture, 452
17.6 Case Histories and Examples of FFS Applications to Cracks in Process Plant Pressure Vessels, 459
References, 464
18 Design of Pressure Vessels and Piping 467
Maher Y. A. Younan
18.1 Modes of Failure, 467
18.2 Basic Stress Analysis, 469
18.3 Design of Pressure Vessels, 470
18.4 Design of Piping Systems, 481
References, 486
19 Process Safety in Chemical Processes 489
Jelenka Savkovic-Stevanovic
19.1 The Hazards, 490
19.2 Hazard Analysis, 499
19.3 Risk Analysis, 503
19.4 Safety Ratings, 511
19.5 Development and Design of a Safe Plant, 524
19.6 Safety Process Operation, 543
19.7 Safety and Reliability Analysis, 557
19.8 Summary, 581
References, 582
SECTION III PROCESS MEASUREMENT, CONTROL, AND MODELING
20 Flowmeters and Measurement 587
Gregory Livelli and Chikezie Nwaoha
20.1 Flow Measurement Techniques, 587
20.2 Flow-Rate Meters, 592
20.3 Common Problems of Flowmeters, 599
20.4 Flowmeter Installation and Maintenance, 601
20.5 Calibration and Certification, 606
20.6 LACT and Prover Descriptions, 607
20.7 Troubleshooting LACT and Prover Systems, 614
20.8 Troubleshooting Flowmeters, 614
References, 617
21 Process Control 619
John A. Shaw
21.1 Control System Components, 619
21.2 Control System Requirements, 620
21.3 Sensor Response, 620
21.4 Control Algorithms, 624
21.5 Loop Tuning, 625
21.6 Multiloop Control, 629
21.7 Final Control Elements, 633
21.8 Process Controllers, 634
Reference, 634
22 Process Modeling and Simulation 635
Mathew Chidiebere Aneke
22.1 Process Modeling, 635
22.2 Process Simulation, 636
22.3 Process Optimization, 636
22.4 Commercial Tools for Process Modeling, Simulation, and Optimization, 637
22.5 Process Modeling Case Studies, 638
22.6 Concluding Remarks, 650
References, 650
Appendix I Methods for Measuring Process Temperature 653
Chikezie Nwaoha
Appendix II Airflow Troubleshooting 659
Chikezie Nwaoha
Appendix III MIG Shielding Gas Control and Optimization 663
Jerry Uttrachi
Appendix IV Rupture Disk Selection 665
Chikezie Nwaoha
Appendix V Pressure Gauge Selection 669
Chikezie Nwaoha
Appendix VI Corrosion and Its Mitigation in the Oil and Gas Industries 673
Krupavaram Nalli
Appendix VII Mixers 681
Jayesh Ramesh Tekchandaney
Glossary of Processing Terms 685
Garlock Sealing Technologies
Index 693
Michael D. Holloway, AS, BA, BS, MS, CLS, has over twenty-five years of industrial experience in lab synthesis, pilot scale manufacturing, product development, application engineering, sales and marketing management, and most recently as Director of Technical Development and Reliability for NCH Corporation. A graduate of Salve Regina College and the University of Massachusetts, he has served as a contributing writer for Manufacturing.net, Assembly, and Plant Services and is the author of Spend Analysis and Specification Development Using Failure Interpretation. He resides in North Texas with his wife and two children.
Chikezie Nwaoha, AMIMechE, MOSHAN, is a petroleum engineer specializing in process engineering/equipment operations, natural gas processing/distribution, and pipeline integrity. He is a contributing editor to both Control Engineering Asia and PetroMin and a downstream correspondent to Petroleum Africa. He worked with Port Harcourt Refining Company (PHRC) in 2005 and 2007 as an industrial trainee. He is also a guest member of the Subsea Integrity Research Group, University of Aberdeen.
OLIVER A. ONYEWUENYI, PE, PhD, is President of MISOL Technology Solutions LLC. He was formerly the program manager of Deepwater Technology/R&D at Shell International and led the award-winning Shell Structural Integrity Analysis Team in Houston. He is the recipient of four industry awards from ASME International and six Shell Special Recognition Awards.
Date de parution : 10-2012
Ouvrage de 728 p.
21.8x28.2 cm