Automation, Production Systems, and Computer-Integrated Manufacturing (5th Ed.)
Auteur : Groover Mikell
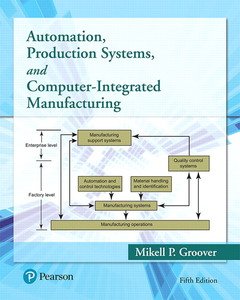
For advanced undergraduate/graduate-level courses in Automation, Production Systems, and Computer-Integrated Manufacturing.
Provides the most up-to-date coverage of automated production systems
Automation, Production Systems, and Computer-Integrated Manufacturing provides up-to-date coverage of production systems, how they are sometimes automated and computerized, and how they can be mathematically analyzed to obtain performance metrics. The text is designed primarily for engineering students at the advanced undergraduate or beginning graduate levels in industrial, mechanical, and manufacturing engineering. The book is also useful for practicing engineers and managers who wish to learn about automation and production systems technologies in modern manufacturing.
This exploration of the technical and engineering aspects of automated production systems provides the most advanced, comprehensive, and balanced coverage of the subject of any text on the market. It covers all the major cutting-edge technologies of production automation and material handling, and how these technologies are used to construct modern manufacturing systems. The 5th Edition has consolidated and reorganized many of the topics, eliminated material that is no longer relevant, and revised end-of-chapter problems.
Table of Contents
- Chapter 1 INTRODUCTION
- 1.1 Production Systems
- 1.2 Automation in Production Systems
- 1.3 Manual Labor in Production Systems
- 1.4 Automation Principles and Strategies
- 1.5 About This Book
PART I OVERVIEW OF MANUFACTURING
- Chapter 2 MANUFACTURING OPERATIONS
- 2.1 Manufacturing Industries and Products
- 2.2 Manufacturing Operations
- 2.3 Production Facilities
- 2.4 Product/Production Relationships
- Chapter 3 MANUFACTURING METRICS AND ECONOMICS
- 3.1 Production Performance Metrics
- 3.2 Manufacturing Costs
PART II AUTOMATION AND CONTROL TECHNOLOGIES
- Chapter 4 INTRODUCTION TO AUTOMATION
- 4.1 Basic Elements of an Automated System
- 4.2 Advanced Automation Functions
- 4.3 Levels of Automation
- 4.4 Automation and Artificial Intelligence
- Chapter 5 INDUSTRIAL CONTROL SYSTEMS
- 5.1 Process Industries versus Discrete Manufacturing Industries
- 5.2 Continuous versus Discrete Control
- 5.3 Computer Process Control
- Chapter 6 HARDWARE COMPONENTS FOR AUTOMATION AND PROCESS CONTROL
- 6.1 Sensors
- 6.2 Actuators
- 6.3 Analog—Digital Conversions
- 6.4 Input/Output Devices for Discrete Data
- Chapter 7 COMPUTER NUMERICAL CONTROL
- 7.1 Fundamentals of NC Technology
- 7.2 Computers and Numerical Control
- 7.3 Applications of NC
- 7.4 Analysis of Positioning Systems
- 7.5 NC Part Programming
- 7.6 CNC Trends and Developments
- Appendix 7A: Coding for Manual Part Programming
- Chapter 8 INDUSTRIAL ROBOTICS
- 8.1 Robot Anatomy and Related Attributes
- 8.2 Robot Control Systems
- 8.3 End Effectors
- 8.4 Applications of Industrial Robots
- 8.5 Economic Justification of Industrial Robots
- 8.6 Robot Programming
- 8.7 Robot Accuracy and Repeatability
- Chapter 9 DISCRETE CONTROL AND PROGRAMMABLE LOGIC CONTROLLERS
- 9.1 Discrete Process Control
- 9.2 Ladder Logic Diagrams
- 9.3 Programmable Logic Controllers
- 9.4 Personal Computers and Programmable Automation Controllers
PART III MATERIAL HANDLING AND IDENTIFICATION
- Chapter 10 MATERIAL TRANSPORT SYSTEMS
- 10.1 Overview of Material Handling
- 10.2 Material Transport Equipment
- 10.3 Analysis of Material Transport Systems
- Chapter 11 STORAGE SYSTEMS
- 11.1 Overview to Storage Systems
- 11.2 Conventional Storage Methods and Equipment
- 11.3 Automated Storage Systems
- 11.4 Analysis of Storage Systems
- Chapter 12 AUTOMATIC IDENTIFICATION AND DATA CAPTURE
- 12.1 Overview of Automatic Identification Methods
- 12.2 Bar Code Technology
PART IV MANUFACTURING SYSTEMS
- Chapter 13 OVERVIEW OF MANUFACTURING SYSTEMS
- 13.1 Components of a Manufacturing System
- 13.2 Types of Manufacturing Systems
- Chapter 14 SINGLE-STATION MANUFACTURING CELLS
- 14.1 Single-Station Manned Cells
- 14.2 Single-Station Automated Cells
- 14.3 Applications of Single-Station Cells
- 14.4 Analysis of Single-Station Cells
- Chapter 15 MULTI-STATION MANUFACTURING SYSTEMS: MANUAL ASSEMBLY LINES
- 15.1 Fundamentals of Manual Assembly Lines
- 15.2 Analysis of Single-Model Assembly Lines
- 15.3 Line Balancing Algorithms
- 15.4 Workstation Details
- 15.5 Other Considerations in Assembly Line Design
- 15.6 Alternative Assembly Systems
- Appendix 15A Batch-Model and Mixed-Model Lines
- Chapter 16 MULTI-STATION MANUFACTURING SYSTEMS: AUTOMATED PRODUCTION LINES
- 16.1 Fundamentals of Automated Production Lines
- 16.2 Applications of Automated Production Lines
- 16.3 Analysis of Transfer Lines
- Appendix 16A Transfer Lines with Internal Storage
- Chapter 17 AUTOMATED ASSEMBLY SYSTEMS
- 17.1 Fundamentals of Automated Assembly Systems
- 17.2 Analysis of Automated Assembly Systems
- Chapter 18 GROUP TECHNOLOGY AND CELLULAR MANUFACTURING
- 18.1 Part Families and Machine Groups
- 18.2 Cellular Manufacturing
- 18.3 Applications of Group Technology
- 18.4 Analysis of Cellular Manufacturing
- Appendix 18A Opitz Parts Classification and Coding System
- Chapter 19 MULTI-STATION MANUFACTURING SYSTEMS: AUTOMATED FOR FLEXIBILITY
- 19.1 Manufacturing Flexibility Defined
- 19.2 Components of an FM
- 19.3 Analysis of Flexible Manufacturing Systems
- 19.4 Alternative Approaches to Flexible Manufacturing
PART V QUALITY CONTROL SYSTEMS
- Chapter 20 QUALITY PROGRAMS FOR MANUFACTURING
- 20.1 Quality in Design and Manufacturing
- 20.2 Traditional and Modern Quality Control
- 20.3 Process Variability and Process Capability
- 20.4 Statistical Process Control
- 20.5 Six Sigma
- 20.6 Taguchi Methods in Quality Engineering
- 20.7 ISO 9000
- Appendix 20A The Six Sigma DMAIC Procedure
- Chapter 21 INSPECTION PRINCIPLES AND PRACTICES
- 21.1 Inspection Fundamentals
- 21.2 Sampling versus 100% Inspection
- 21.3 Automated Inspection
- 21.4 When and Where to Inspect
- 21.5 Analysis of Inspection Systems
- Chapter 22 INSPECTION TECHNOLOGIES
- 22.1 Inspection Metrology
- 22.2 Conventional Measuring and Gaging Techniques
- 22.3 Coordinate Measuring Machines
- 22.4 Surface Measurement
- 22.5 Machine Vision
- 22.6 Other Optical Inspection Methods
- 22.7 Noncontact Nonoptical Inspection Techniques
- Appendix 22A Geometric Feature Construction
PART VI MANUFACTURING SUPPORT SYSTEMS AND COMPUTER-INTEGRATED MANUFACTURING
- Chapter 23 PRODUCT DESIGN AND CAD/CAM IN THE PRODUCTION SYSTEM
- 23.1 Product Design and CAD
- 23.2 CAM, CAD/CAM, and CIM
- Chapter 24 PROCESS PLANNING AND CONCURRENT ENGINEERING
- 24.1 Process Planning
- 24.2 Computer-Aided Process Planning
- 24.3 Concurrent Engineering and Design for Manufacturing
- 24.4 Advanced Manufacturing Planning
- Chapter 25 PRODUCTION PLANNING AND CONTROL SYSTEMS
- 25.1 Aggregate Production Planning and the Master Production Schedule
- 25.2 Material Requirements Planning
- 25.3 Capacity Planning
- 25.4 Shop Floor Control
- 25.5 Inventory Control
- 25.6 Manufacturing Resource Planning (MRP II)
- 25.7 Enterprise Resource Planning (ERP)
- Chapter 26 JUST-IN-TIME AND LEAN PRODUCTION
- 26.1 Lean Production and Waste in Manufacturing
- 26.2 Just-in-Time Production Systems
- 26.3 Autonomation
- 26.4 Worker Involvement
Appendix Answers to Selected Problems
About our author
Mikell P. Groover is Professor Emeritus of Industrial and Systems Engineering at Lehigh University, where he taught and did research for 44 years. He received his B.A. in Arts and Science (1961), B.S. in Mechanical Engineering (1962), M.S. in Industrial Engineering (1966), and Ph.D. (1969), all from Lehigh. His industrial experience includes several years as a manufacturing engineer before embarking on graduate studies.
His teaching and research areas include manufacturing processes, production systems, automation, material handling, facilities planning, and work systems. He has received a number of teaching awards at Lehigh University, as well as the Albert G. Holzman Outstanding Educator Award from the Institute of Industrial Engineers (1995) and the SME Education Award from the Society of Manufacturing Engineers (2001). His publications include over 85 technical articles and books. His books are used throughout the world and have been translated into French, German, Spanish, Portuguese, Russian, Japanese, Korean and Chinese. The 1st edition of Fundamentals of Modern Manufacturing received the IIE Joint Publishers Award (1996) and the M. Eugene Merchant Manufacturing Textbook Award from the Society of Manufacturing Engineers (1996).
Dr. Groover is a member of the Institute of Industrial Engineers (IIE) and the Society of Manufacturing Engineers (SME). He is a Fellow of IIE and SME.
Provide a balanced approach to automated production systems
- A quantitative approach provides numerous equations and example problems for instructors who want to include analytical and quantitative material in their courses.
- “What the Equations Tell Us” statements follow the mathematical derivations and engineering equations. These statements list the practical meanings of the equations and guidelines regarding applications.
- Historical notes and vignettes describe the development and historical background of the automation technologies.
Support problem solving and learning
- Revised - More than 40% of the end-of-chapter problems are revised. There are now a total of 413 end-of-chapter review questions and 408 end-of-chapter problems in the book.
- Application guidelines are included in several of the descriptions of the technologies.
- A total of 99 example problems illustrating many problem types are included in the text coverage.
Provides the most up-to-date content of automated production systems
- New - An Automation and Artificial Intelligence section has been added in Chapter 4.
- New - CNC Trends and Developments section has been added to Chapter 7 (Computer Numerical Control).
- New - Collaborative Robotssection has been added to Chapter 8 (Industrial Robotics).
- Revised and Expanded - CNC Machining Centers and Related Machine Tools Coverage in Chapter 14 has been updated, and several new line drawings have been added.
- Revised - Discussion and analysisreflect changes inFMS technology in Chapter 19.
- Revised - Surface measurement section in Chapter 22 (Inspection Technologies) incl
Date de parution : 09-2020
Ouvrage de 816 p.