Advanced Chemical Process Control Putting Theory into Practice
Auteur : Hovd Morten
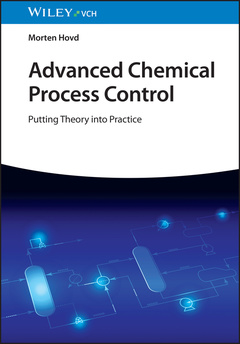
Bridge the gap between theory and practice with this accessible guide
Process control is an area of study which seeks to optimize industrial processes, applying different strategies and technologies as required to navigate the variety of processes and their many potential challenges. Though the body of chemical process control theory is robust, it is only in recent decades that it has been effectively integrated with industrial practice to form a flexible toolkit. The need for a guide to this integration of theory and practice has therefore never been more urgent.
Advanced Chemical Process Control meets this need, making advanced chemical process control accessible and useful to chemical engineers with little grounding in the theoretical principles of the subject. It provides a basic introduction to the background and mathematics of control theory, before turning to the implementation of control principles in industrial contexts. The result is a bridge between the insights of control theory and the needs of engineers in plants, factories, research facilities, and beyond.
Advanced Chemical Process Control readers will also find:
- Detailed overview of Control Performance Monitoring (CPM), Model Predictive Control (MPC), and more
- Discussion of the cost benefit analysis of improved control in particular jobs
- Authored by a leading international expert on chemical process control
Advanced Chemical Process Control is essential for chemical and process engineers looking to develop a working knowledge of process control, as well as for students and graduates entering the chemical process control field.
Preface xvii
Acknowledgments xxi
Acronyms xxiii
Introduction xxv
1 Mathematical and Control Theory Background 1
1.1 Introduction 1
1.2 Models for Dynamical Systems 1
1.2.1 Dynamical Systems in Continuous Time 1
1.2.2 Dynamical Systems in Discrete Time 2
1.2.3 Linear Models and Linearization 3
1.2.3.1 Linearization at a Given Point 3
1.2.3.2 Linearizing Around a Trajectory 6
1.2.4 Converting Between Continuous- and Discrete-Time Models 6
1.2.4.1 Time Delay in the Manipulated Variables 7
1.2.4.2 Time Delay in the Measurements 9
1.2.5 Laplace Transform 9
1.2.6 The z Transform 10
1.2.7 Similarity Transformations 11
1.2.8 Minimal Representation 11
1.2.9 Scaling 14
1.3 Analyzing Linear Dynamical Systems 15
1.3.1 Transfer Functions of Composite Systems 15
1.3.1.1 Series Interconnection 15
1.3.1.2 Parallel Systems 16
1.3.1.3 Feedback Connection 16
1.3.1.4 Commonly Used Closed-Loop Transfer Functions 17
1.3.1.5 The Push-Through Rule 17
1.4 Poles and Zeros of Transfer Functions 18
1.4.1 Poles of Multivariable Systems 19
1.4.2 Pole Directions 19
1.4.3 Zeros of Multivariable Systems 20
1.4.4 Zero Directions 22
1.5 Stability 23
1.5.1 Poles and Zeros of Discrete-Time Transfer Functions 23
1.5.2 Frequency Analysis 24
1.5.2.1 Steady-State Phase Adjustment 26
1.5.3 Bode Diagrams 27
1.5.3.1 Bode Diagram Asymptotes 27
1.5.3.2 Minimum Phase Systems 29
1.5.3.3 Frequency Analysis for Discrete-Time Systems 30
1.5.4 Assessing Closed-Loop Stability Using the Open-Loop Frequency Response 31
1.5.4.1 The Principle of the Argument and the Nyquist D-Contour 31
1.5.4.2 The Multivariable Nyquist Theorem 32
1.5.4.3 The Monovariable Nyquist Theorem 32
1.5.4.4 The Bode Stability Criterion 32
1.5.4.5 Some Remarks on Stability Analysis Using the Frequency Response 35
1.5.4.6 The Small Gain Theorem 36
1.5.5 Controllability 37
1.5.6 Observability 38
1.5.7 Some Comments on Controllability and Observability 39
1.5.8 Stabilizability 40
1.5.9 Detectability 40
1.5.10 Hidden Modes 41
1.5.11 Internal Stability 41
1.5.12 Coprime Factorizations 43
1.5.12.1 Inner–Outer Factorization 44
1.5.12.2 Normalized Coprime Factorization 44
1.5.13 Parametrization of All Stabilizing Controllers 44
1.5.13.1 Stable Plants 45
1.5.13.2 Unstable Plants 45
1.5.14 Hankel Norm and Hankel Singular Values 46
Problems 47
References 49
2 Control Configuration and Controller Tuning 51
2.1 Common Control Loop Structures for the Regulatory Control Layer 51
2.1.1 Simple Feedback Loop 51
2.1.2 Feedforward Control 51
2.1.3 Ratio Control 54
2.1.4 Cascade Control 54
2.1.5 Auctioneering Control 55
2.1.6 Split Range Control 56
2.1.7 Input Resetting Control 57
2.1.8 Selective Control 59
2.1.9 Combining Basic Single-Loop Control Structures 60
2.1.10 Decoupling 61
2.2 Input and Output Selection 62
2.2.1 Using Physical Insights 63
2.2.2 Gramian-Based Input and Output Selection 64
2.2.3 Input/Output Selection for Stabilization 65
2.3 Control Configuration 66
2.3.1 The Relative Gain Array 66
2.3.2 The RGA as a General Analysis Tool 68
2.3.2.1 The RGA and Zeros in the Right Half-Plane 68
2.3.2.2 The RGA and the Optimally Scaled Condition Number 68
2.3.2.3 The RGA and Individual Element Uncertainty 69
2.3.2.4 RGA and Diagonal Input Uncertainty 69
2.3.2.5 The RGA as an Interaction Measure 70
2.3.3 The RGA and Stability 70
2.3.3.1 The RGA and Pairing of Controlled and Manipulated Variables 71
2.3.4 Summary of RGA-Based Input–Output Pairing 72
2.3.5 Partial Relative Gains 72
2.3.6 The Niederlinski Index 73
2.3.7 The Rijnsdorp Interaction Measure 73
2.3.8 Gramian-Based Input–Output Pairing 74
2.3.8.1 The Participation Matrix 75
2.3.8.2 The Hankel Interaction Index Array 75
2.3.8.3 Accounting for the Closed-Loop Bandwidth 76
2.4 Tuning of Decentralized Controllers 76
2.4.1 Introduction 76
2.4.2 Loop Shaping Basics 77
2.4.3 Tuning of Single-Loop Controllers 79
2.4.3.1 PID Controller Realizations and Common Modifications 79
2.4.3.2 Controller Tuning Using Frequency Analysis 81
2.4.3.3 Ziegler–Nichols Closed-Loop Tuning Method 86
2.4.3.4 Simple Fitting of a Step Response Model 86
2.4.3.5 Ziegler–Nichols Open-Loop Tuning 88
2.4.3.6 IMC-PID Tuning 88
2.4.3.7 Simple IMC Tuning 89
2.4.3.8 The Setpoint Overshoot Method 91
2.4.3.9 Autotuning 95
2.4.3.10 When Should Derivative Action Be Used? 95
2.4.3.11 Effects of Internal Controller Scaling 96
2.4.3.12 Reverse Acting Controllers 97
2.4.4 Gain Scheduling 97
2.4.5 Surge Attenuating Controllers 98
2.4.6 Multiloop Controller Tuning 99
2.4.6.1 Independent Design 100
2.4.6.2 Sequential Design 102
2.4.6.3 Simultaneous Design 103
2.4.7 Tools for Multivariable Loop-Shaping 103
2.4.7.1 The Performance Relative Gain Array 103
2.4.7.2 The Closed-Loop Disturbance Gain 104
2.4.7.3 Illustrating the Use of CLDG’s for Controller Tuning 104
2.4.7.4 Unachievable Loop Gain Requirements 107
Problems 108
References 112
3 Control Structure Selection and Plantwide Control 115
3.1 General Approach and Problem Decomposition 115
3.1.1 Top-Down Analysis 115
3.1.1.1 Defining and Exploring Optimal Operation 115
3.1.1.2 Determining Where to Set the Throughput 116
3.1.2 Bottom-Up Design 116
3.2 Regulatory Control 117
3.2.1 Example: Regulatory Control of Liquid Level in a Deaeration Tower 118
3.3 Determining Degrees of Freedom 121
3.4 Selection of Controlled Variables 122
3.4.1 Problem Formulation 123
3.4.2 Selecting Controlled Variables by Direct Evaluation of Loss 124
3.4.3 Controlled Variable Selection Based on Local Analysis 125
3.4.3.1 The Minimum Singular Value Rule 127
3.4.3.2 Desirable Characteristics of the Controlled Variables 128
3.4.4 An Exact Local Method for Controlled Variable Selection 128
3.4.5 Measurement Combinations as Controlled Variables 130
3.4.5.1 The Nullspace Method for Selecting Controlled Variables 130
3.4.5.2 Extending the Nullspace Method to Account for Implementation Error 130
3.4.6 The Validity of the Local Analysis for Controlled Variable Selection 131
3.5 Selection of Manipulated Variables 132
3.5.1 Verifying that the Proposed Manipulated Variables Make Acceptable Control Possible 133
3.5.2 Reviewing the Characteristics of the Proposed Manipulated Variables 134
3.6 Selection of Measurements 135
3.7 Mass Balance Control and Throughput Manipulation 136
3.7.1 Consistency of Inventory Control 138
Problems 140
References 141
4 Limitations on Achievable Performance 143
4.1 Performance Measures 143
4.1.1 Time-Domain Performance Measures 143
4.1.2 Frequency-Domain Performance Measures 145
4.1.2.1 Bandwidth Frequency 145
4.1.2.2 Peaks of Closed-Loop Transfer Functions 146
4.1.2.3 Bounds on Weighted System Norms 146
4.1.2.4 Gain and Phase Margin 147
4.2 Algebraic Limitations 148
4.2.1 S + T = I 148
4.2.2 Interpolation Constraints 148
4.2.2.1 Monovariable Systems 148
4.2.2.2 Multivariable Systems 149
4.3 Control Performance in Different Frequency Ranges 149
4.3.1 Sensitivity Integrals and Right Half-Plane Zeros 149
4.3.1.1 Multivariable Systems 150
4.3.2 Sensitivity Integrals and Right Half-Plane Poles 150
4.3.3 Combined Effects of RHP Poles and Zeros 150
4.3.4 Implications of the Sensitivity Integral Results 150
4.4 Bounds on Closed-Loop Transfer Functions 151
4.4.1 The Maximum Modulus Principle 152
4.4.1.1 The Maximum Modulus Principle 152
4.4.2 Minimum Phase and Stable Versions of the Plant 152
4.4.3 Bounds on S and T 153
4.4.3.1 Monovariable Systems 153
4.4.3.2 Multivariable Systems 153
4.4.4 Bounds on KS and KSG d 154
4.5 ISE Optimal Control 156
4.6 Bandwidth and Crossover Frequency Limitations 156
4.6.1 Bounds from ISE Optimal Control 156
4.6.2 Bandwidth Bounds from Weighted Sensitivity Minimization 157
4.6.3 Bound from Negative Phase 158
4.7 Bounds on the Step Response 158
4.8 Bounds for Disturbance Rejection 160
4.8.1 Inputs for Perfect Control 161
4.8.2 Inputs for Acceptable Control 161
4.8.3 Disturbances and RHP Zeros 161
4.8.4 Disturbances and Stabilization 162
4.9 Limitations from Plant Uncertainty 164
4.9.1 Describing Uncertainty 165
4.9.2 Feedforward Control and the Effects of Uncertainty 166
4.9.3 Feedback and the Effects of Uncertainty 167
4.9.4 Bandwidth Limitations from Uncertainty 168
Problems 168
References 170
5 Model-Based Predictive Control 173
5.1 Introduction 173
5.2 Formulation of a QP Problem for MPC 175
5.2.1 Future States as Optimization Variables 179
5.2.2 Using the Model Equation to Substitute for the Plant States 180
5.2.3 Optimizing Deviations from Linear State Feedback 181
5.2.4 Constraints Beyond the End of the Prediction Horizon 182
5.2.5 Finding the Terminal Constraint Set 183
5.2.6 Feasible Region and Prediction Horizon 184
5.3 Step-Response Models 185
5.4 Updating the Process Model 186
5.4.1 Bias Update 186
5.4.2 Kalman Filter and Extended Kalman Filters 187
5.4.2.1 Augmenting a Disturbance Description 188
5.4.2.2 The Extended Kalman Filter 189
5.4.2.3 The Iterated Extended Kalman Filter 189
5.4.3 Unscented Kalman Filter 190
5.4.4 Receding Horizon Estimation 193
5.4.4.1 The Arrival Cost 195
5.4.4.2 The Filtering Formulation of RHE 196
5.4.4.3 The Smoothing Formulation of RHE 196
5.4.5 Concluding Comments on State Estimation 198
5.5 Disturbance Handling and Offset-Free Control 199
5.5.1 Feedforward from Measured Disturbances 199
5.5.2 Requirements for Offset-Free Control 199
5.5.3 Disturbance Estimation and Offset-Free Control 200
5.5.4 Augmenting the Model with Integrators at the Plant Input 203
5.5.5 Augmenting the Model with Integrators at the Plant Output 205
5.5.6 MPC and Integrator Resetting 208
5.6 Feasibility and Constraint Handling 210
5.7 Closed-Loop Stability with MPC Controllers 212
5.8 Target Calculation 213
5.9 Speeding up MPC Calculations 217
5.9.1 Warm-Starting the Optimization 218
5.9.2 Input Blocking 219
5.9.3 Enlarging the Terminal Region 220
5.10 Robustness of MPC Controllers 222
5.11 Using Rigorous Process Models in MPC 225
5.12 Misconceptions, Clarifications, and Challenges 226
5.12.1 Misconceptions 226
5.12.1.1 MPC Is Not Good for Performance 226
5.12.1.2 MPC Requires Very Accurate Models 227
5.12.1.3 MPC Cannot Prioritize Input Usage or Constraint Violations 227
5.12.2 Challenges 227
5.12.2.1 Obtaining a Plant Model 228
5.12.2.2 Maintenance 228
5.12.2.3 Capturing the Desired Behavior in the MPC Design 228
Problems 228
References 231
6 Some Practical Issues in Controller Implementation 233
6.1 Discrete-Time Implementation 233
6.1.1 Aliasing 233
6.1.2 Sampling Interval 233
6.1.3 Execution Order 235
6.2 Pure Integrators in Parallel 235
6.3 Anti-Windup 236
6.3.1 Simple PI Control Anti-Windup 237
6.3.2 Velocity Form of PI Controllers 237
6.3.3 Anti-Windup in Cascaded Control Systems 238
6.3.4 A General Anti-Windup Formulation 239
6.3.5 Hanus’ Self-Conditioned Form 240
6.3.6 Anti-Windup in Observer-Based Controllers 241
6.3.7 Decoupling and Input Constraints 243
6.3.8 Anti-Windup for “Normally Closed” Controllers 244
6.4 Bumpless Transfer 245
6.4.1 Switching Between Manual and Automatic Operation 245
6.4.2 Changing Controller Parameters 246
Problems 246
References 247
7 Controller Performance Monitoring and Diagnosis 249
7.1 Introduction 249
7.2 Detection of Oscillating Control Loops 251
7.2.1 The Autocorrelation Function 251
7.2.2 The Power Spectrum 252
7.2.3 The Method of Miao and Seborg 252
7.2.4 The Method of Hägglund 253
7.2.5 The Regularity Index 254
7.2.6 The Method of Forsman and Stattin 255
7.2.7 Prefiltering Data 255
7.3 Oscillation Diagnosis 256
7.3.1 Manual Oscillation Diagnosis 256
7.3.2 Detecting and Diagnosing Valve Stiction 257
7.3.2.1 Using the Cross-Correlation Function to Detect Valve Stiction 257
7.3.2.2 Histograms for Detecting Valve Stiction 258
7.3.2.3 Stiction Detection Using an OP–PV Plot 260
7.3.3 Stiction Compensation 262
7.3.4 Detection of Backlash 263
7.3.5 Backlash Compensation 264
7.3.6 Simultaneous Stiction and Backlash Detection 265
7.3.7 Discriminating Between External and Internally Generated Oscillations 266
7.3.8 Detecting and Diagnosing Other Nonlinearities 266
7.4 Plantwide Oscillations 269
7.4.1 Grouping Oscillating Variables 269
7.4.1.1 Spectral Principal Component Analysis 269
7.4.1.2 Visual Inspection Using High-Density Plots 269
7.4.1.3 Power Spectral Correlation Maps 270
7.4.1.4 The Spectral Envelope Method 271
7.4.1.5 Methods Based on Adaptive Data Analysis 272
7.4.2 Locating the Cause for Distributed Oscillations 273
7.4.2.1 Using Nonlinearity for Root Cause Location 273
7.4.2.2 The Oscillation Contribution Index 273
7.4.2.3 Estimating the Propagation Path for Disturbances 274
7.5 Control Loop Performance Monitoring 278
7.5.1 The Harris Index 278
7.5.2 Obtaining the Impulse Response Model 279
7.5.3 Calculating the Harris Index 280
7.5.4 Estimating the Deadtime 281
7.5.5 Modifications to the Harris Index 282
7.5.6 Assessing Feedforward Control 283
7.5.7 Comments on the Use of the Harris Index 285
7.5.8 Performance Monitoring for PI Controllers 286
7.6 Multivariable Control Performance Monitoring 287
7.6.1 Assessing Feedforward Control in Multivariable Control 287
7.6.2 Performance Monitoring for MPC Controllers 288
7.7 Some Issues in the Implementation of Control Performance Monitoring 290
7.8 Discussion 290
Problems 291
References 291
8 Economic Control Benefit Assessment 297
8.1 Optimal Operation and Operational Constraints 297
8.2 Economic Performance Functions 298
8.3 Expected Economic Benefit 299
8.4 Estimating Achievable Variance Reduction 300
8.5 Worst-Case Backoff Calculation 300
References 301
A Fourier–Motzkin Elimination 303
B Removal of Redundant Constraints 307
Reference 308
C The Singular Value Decomposition 309
D Factorization of Transfer Functions into Minimum Phase Stable and All-Pass Parts 311
D. 1 Input Factorization of RHP Zeros 312
D. 2 Output Factorization of RHP Zeros 312
D. 3 Output Factorization of RHP Poles 313
D. 4 Input Factorization of RHP Poles 313
D. 5 SISO Systems 314
D. 6 Factoring Out Both RHP Poles and RHP Zeros 314
Reference 314
E Models Used in Examples 315
E.1 Binary Distillation Column Model 315
E.2 Fluid Catalytic Cracker Model 318
References 320
Index 321
Morten Hovd, PhD, is Professor of Process Control at the Department of Engineering and Cybernetics, Norwegian University of Science and Technology, Trondheim, Norway. He is a member of the IEEE Technical Committee on Process Control and the International Federation of Automatic Control (IFAC) Technical Committee on Mining, Minerals, and Metals Processing, and has over 150 scientific publications.
Date de parution : 06-2023
Ouvrage de 368 p.
17x24.4 cm