Underbalanced Drilling: Limits and Extremes Gulf Drilling Guides Series
Coordonnateurs : Rehm Bill, Haghshenas Arash, Paknejad Amir Saman, Al-Yami Abdullah, Hughes Jim
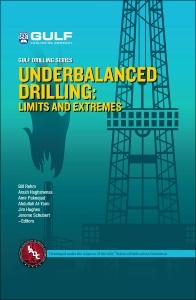
The present crude oil and natural gas reservoirs around the world have depleted conventional production levels. To continue enhancing productivity for the remaining mature reservoirs, drilling decision-makers could no longer rely on traditional balanced or overbalanced methods of drilling. Derived from conventional air drilling, underbalanced drilling is increasingly necessary to meet today?s energy and drilling needs. While more costly and extreme, underbalanced drilling can minimize pressure within the formation, increase drilling rate of penetration, reduce formation damage and lost circulation, making mature reservoirs once again viable and more productive. To further explain this essential drilling procedure, Bill Rehm, an experienced legend in drilling along with his co-editors, has compiled a handbook perfect for the drilling supervisor.
Underbalanced Drilling: Limits and Extremes, written under the auspices of the IADC Technical Publications Committee, contain many great features and contributions including:
- Real case studies shared by major service companies to give the reader guidelines on what might happen in actual operations
- Questions and answers at the end of the chapters for upcoming engineers to test their knowledge
- Common procedures, typical and special equipment involved, and most importantly, the limits and challenges that still surround this technology
List of Tables
Foreword
Preface
1 Piping Codes, Standards, and Specifications
1.1 Introduction
1.2 Definitions
1.3 Codes
1.3.1 American Society of Mechanical Engineers Boiler Pressure Vessel Codes
1.3.2 American Society of Mechanical Engineers B31, Codes for Pressure Piping
1.4 Standards and Specifications
1.4.1 American Society of Mechanical Engineers
1.4.2 American Petroleum Institute
1.4.3 American Society for Testing and Materials
1.4.4 American Society for Nondestructive Testing
1.4.5 American Society for Quality
1.4.6 American Welding Society
1.4.7 American Water Works Association
1.4.8 Copper Development Association
1.4.9 Compressed Gas Association
1.4.10 Canadian Standards Association
1.4.11 Expansion Joint Manufacturers Association
1.4.12 Manufacturers Standardization Society of the Valve and Fittings Industry
1.4.13 National Association of Corrosion Engineers
1.4.14 National Fire Protection Association
1.4.15 Pipe Fabrication Institute
1.4.16 Society of Automotive Engineers
2 Piping Components
2.1 Introduction to Piping Components
2.2 Pipe
2.2.1 Pipe Sizes
2.2.2 Pipe Ends
2.3 Pipe Fittings
2.3.1 Butt-Weld End Fittings
2.3.2 Socket-Weld and Threaded-End Fittings
2.3.3 Flanged Joints
2.4 Valves
2.4.1 Valve Codes and Standards
2.4.2 Classification of Operation Valves
2.4.3 Valve Classification
2.4.4 Valve Components
2.5 Bolts and Gaskets (Fasteners and Sealing Elements)
2.5.1 The Process of Joint Integrity
2.5.2 Flange Joint Components
2.5.3 The Flanged Joint System
3 Metallic Materials for Piping Components
3.1 Properties of Piping Materials
3.1.1 Chemical Properties of Metals
3.1.2 Mechanical Properties of Metals
3.1.3 Elongation and Reduction of Area
3.1.4 Physical Properties of Metals
3.2 Metallic Materials
3.3 Alloying of Steel
3.4 Types of Steel
3.4.1 Mild (Low-Carbon) Steel
3.4.2 Medium-Carbon Steel
3.4.3 High-Carbon Steel
3.4.4 High-Tensile Steel
3.4.5 Stainless Steel
3.5 Steel Heat-Treating Methods
3.5.1 Annealing
3.5.2 Normalizing
3.5.3 Hardening
3.5.4 Tempering
3.6 Nonferrous Metals in Alloying
3.7 Material Specifications
3.7.1 American Society for Testing and Materials
3.7.2 Unified Numbering System of Ferrous Metals and Alloys
4 Roles and Responsibilities
4.1 The Lead Piping Engineer
4.2 Piping Materials Engineering Group
4.2.1 Project Lead Piping Materials Engineer
4.2.2 Senior Piping Materials Engineer
4.3 Piping Design Group
4.3.1 Project Piping Area/Unit Supervisor (Squad Boss)
4.3.2 Project Piping CAD Coordinator
4.3.3 Project Piping Designers-Checkers
4.4 Piping Materials Control Group
4.4.1 Project Lead Piping Materials Controller
4.4.2 Project Piping Materials Controller
4.5 Piping Stress Engineering Group
4.5.1 Project Lead Piping Stress Engineer
4.5.2 Project Piping Stress Engineer
4.6 Other Engineering Disciplines Involved
4.6.1 Process Engineering
4.6.2 Mechanical Engineering
4.6.3 Instrument Engineering
4.6.4 Civil Engineering
4.6.5 Structural Engineering
5 Projects
5.1 Project Types
5.2 Project Phases
5.2.1 Feasibility Phase
5.2.2 Conception Phase
5.2.3 Front-End Engineering Development Phase
5.2.4 Detailed Engineering Phase
5.2.5 Construction Phase
5.2.6 Precommissioning and Commissioning Phase
5.2.7 Startup and Handover to the Owner
6 Fabrication, Assembly, and Erection
6.1 Codes and Standards Considerations
6.2 Fabrication Materials for Piping Systems
6.3 Fabrication Drawings
6.4 Fabrication Activities
6.4.1 Cutting
6.4.2 Beveling
6.4.3 Forming
6.4.4 Bending
6.5 Welding
6.5.1 Welding Processes
6.5.2 Preheating
6.5.3 Heat Treatment
6.6 Brazing and Soldering
6.7 Protection of Carbon Steel in Corrosive Services
6.7.1 Corrosion Allowance
6.7.2 Internal Galvanizing of Pipe and Piping Systems
6.7.3 Pipe Cladding
6.8 Assembly and Erection
6.8.1 Alignment
6.8.2 Flanged Joints
6.8.3 Threaded Joints
7 Inspection and Testing
7.1 Piping Codes
7.2 Types of Examination
7.2.1 Visual Examination
7.2.2 Liquid Penetrant Examination
7.2.3 Magnetic Particle Examination
7.2.4 Radiographic Examination
7.2.5 Ultrasonic Examination
7.3 Testing of Piping Systems
7.3.1 Some Limitations on the Pressure Testing of Piping Systems
7.3.2 Special Provisions for Testing
7.3.3 Preparation for Leak Test
7.4 Leak-Testing Methods
7.4.1 Hydrostatic Leak Test
7.4.2 Pneumatic Leak Test
7.4.3 Combination Hydrostatic-Pneumatic Leak Test
7.4.4 Initial Service Leak Testing
7.5 Choice of Testing Medium
7.6 Test Pack
7.7 Punch List
A Listed Material
A.0.1 Ferrous Metals
A.0.2 Nonferrous Material
A.1 American Petroleum Institute
B General Engineering Data
Index
Date de parution : 05-2012
Ouvrage de 629 p.
15.2x22.8 cm
Thèmes d’Underbalanced Drilling: Limits and Extremes :
Mots-clés :
engineering; pipe size; joints; metallic materials; steel; nonferrous metals; fabrication