Plastics Product Design
Auteur : Mastro Paul F.
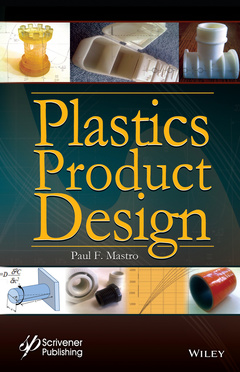
Provides the reader with access to lessons learned in the author?s 40 years of plastics product design experience
Part 1 of the book provides the reader with an introduction to plastics as a design material and a discussion of materials commonly in use today. There is a discussion of a variety of processes available to the designer to make a part along with the design considerations each process will entail. This section also includes a discussion of useful prototyping processes, including advantages and disadvantages of each. Next, the book discusses general design considerations applicable to most plastics product designs.
In Part 2 of the book the author discusses elements of design of a number of generic plastic product types based on his more than 40 years of experience of product design and development for several companies with a variety of products. This section includes discussions of structural components, gears, bearings, hinges, snap fits, packaging, pressure vessels, and optical components. This section also discusses the general considerations that apply to these applications as well as specific insights about each particular application. There is also a chapter on the most important joining techniques. Part 2 ends with a discussion of the general design process.
The book concludes with 3 appendices on thermal properties of selected generic materials; properties of selected structural components; and common abbreviations for plastic materials.
Audience
This book is aimed at product designers and plastics application engineers who have had limited or no experience with plastics materials as well as a more experienced designer who is designing a part for a use, process or an application that they are not familiar with.
Preface xi
PART 1: Plastics as a Design Material 1
1 Introduction to Plastics Materials 3
1.1 History of Plastics 3
1.2 Definition of Plastics 5
1.3 Thermoplastics and Thermosets 5
1.4 How Plastics are Made 6
1.5 General Plastics Properties 7
1.6 Plastics Feedstocks and Volumes 8
2 Properties of Plastics 11
2.1 Molecular Weight and Molecular Weight Distribution 13
2.2 Melt Flow Index 16
2.3 Molecular Structure of Polymers 16
2.4 Thermal Properties of Plastics 17
2.5 Physical Properties of Plastics 24
2.6 Electrical Properties 28
2.7 Flammability 29
3 Overview of Plastics Materials 31
3.1 Polyethylene 32
3.2 Polypropylene 35
3.3 Polystyrene 37
3.4 Polyvinyl Chloride 39
3.5 Engineering Plastics 41
3.5.1 Cellulosics 41
3.5.2 Polymethyl Methacrylate (Acrylic) 42
3.5.3 Polycarbonates 43
3.5.4 Polyamides (Nylon) 45
3.5.5 Polyoxymethylene (Acetal) 46
3.5.6 Thermoplastic Polyesters 47
3.5.7 Fluoropolymers 48
3.5.8 High Performance Polymers 49
3.5.8.1 Polyphenylenes 50
3.5.8.2 Polysulfones 50
3.5.8.3 Polyaramids 51
3.5.8.4 Polyarylether Ketones 51
3.5.8.5 Liquid Crystal Polymers (LCPs) 52
3.5.8.6 Th ermoplastic Polyimides 53
3.5.8.7 Polybenzimidazole 53
3.6 Thermoplastic Elastomers 54
3.7 Biopolymers 55
3.7.1 Polylactic Acid 55
3.7.2 Polyhydroxyalkanoates 56
3.7.3 Polybutylene Succinate 56
3.8 Thermosets 56
3.8.1 Phenolics 57
3.8.2 Amino Plastics 57
3.8.3 Epoxies 59
3.8.4 Thermoset Polyesters 60
3.8.5 Thermoset Polyurethanes 61
3.8.6 Polydicyclopentadiene 62
3.8.7 Thermoset Polyimides 62
3.9 Fillers and Reinforcements 62
4 Process Overviews, Advantages and Constraints 65
4.1 Extrusion 66
4.2 Injection Molding 69
4.3 Extrusion Blow Molding 76
4.4 Injection Blow Molding and Stretch Blow Molding 78
4.5 Compression Molding 81
4.6 Transfer Molding 82
4.7 Rotational Molding 82
4.8 Reaction Injection Molding 85
4.9 Thermoforming 85
4.10 Filament Winding 87
4.11 Pultrusion 89
4.12 Additive Manufacturing (3D Printing) 90
4.13 Other Prototyping Processes 92
5 General Design Considerations 93
5.1 Shrinkage 93
5.2 Dimensional Tolerances 94
5.3 Draft 98
5.4 Gating 100
5.5 Coring and Holes 102
5.6 Rib Design 106
5.7 Color and Appearance 107
5.8 Chemical Resistance 109
5.9 Weathering and Environmental Effects 111
5.10 Recycling and Recycling Codes 112
PART 2: Plastics Product Design 115
6 Structural Components 117
6.1 Rigidity and Strength 118
6.2 Creep 120
6.3 Fatigue 130
6.4 Torsion 131
6.5 Impact 134
6.6 Other Elevated Temperature Considerations 137
7 Enclosures 139
7.1 Cosmetics 140
7.2 Structural Support 142
7.3 Ventilation 148
7.4 Flammability 149
7.5 Electrical Considerations 152
8 Packaging and Containers 157
8.1 Impact and Tear Resistance 157
8.2 Strength and Rigidity 158
8.3 Barrier Properties 158
8.4 Packaging Processes 162
8.5 Printing and Decorating 165
9 Snap Fits and Hinges 169
9.1 Snap Fit Designs 170
9.2 Design of Cantilever Snaps Using Classical Beam Theory 172
9.3 Assembly and Disassembly 180
9.4 Non-Rectangular Cantilevered Beams 186
9.5 Effects of Stress Concentration 186
9.6 Annular Snap Fits 187
9.7 Manufacturability 190
9.8 Plastic Hinges 192
10 Plastic Gears 195
10.1 How Gears Work 196
10.2 Types of Gears 198
10.3 Terminology 201
10.4 Gear Tooth Loading 203
10.5 Contact Stress 208
10.6 Gear Tolerances 209
10.7 Gear Tooth Design 211
10.8 Gear Mesh Conditions and Operating Distances 213
10.9 Software 216
10.10 Prototyping 217
10.11 Gear Manufacturability 217
10.12 Gear Materials 221
11 Bearings 223
11.1 Wear 225
11.2 Bearing Life and Performance 228
11.3 Bearing Design 230
11.4 Bearing Materials 230
12 Pressure Vessels and Pipes 233
12.1 Pipe 234
12.2 Miner’s Rule 237
12.3 Other Pressure Vessels 239
12.4 Other Types of Pressure Vessels 243
12.5 Material and Manufacturing Considerations 243
13 Plastic Optics 247
13.1 Optical Fundamentals 247
13.2 Mirrors 252
13.3 Light Pipes 254
13.4 Lenses 254
13.5 Manufacturing Processes for Optical Components 256
13.6 Measuring Techniques 257
14 Joining Techniques 259
14.1 Threads and Threading 260
14.2 Self-Tapping Screws 263
14.3 Metal Inserts 265
14.4 Ultrasonic Welding 268
14.5 Vibration and Hot Plate Welding 272
14.6 Spin Welding 274
14.7 Solvent and Adhesive Bonding 275
14.8 Bolt and Screw Assembly 278
15 Product Design Process 281
15.1 Design Process 281
15.2 Material Selection 289
15.3 Design Services 289
Appendix A Thermal Properties of Selected Generic Materials 293
Appendix B Properties of Selected Structural Components 295
Appendix C Common Abbreviations for Plastic Materials 297
References 299
Index 303
Paul Mastro has worked in the plastics industry for over 40 years in a variety of capacities including corporate officer of a major international company, international experience and managerial positions in engineering, R&D, operations and marketing. He started two grass roots manufacturing operations. Paul currently is the principal of Paul Mastro LLC and provides expertise in plastics materials, manufacturing productivity, product innovation, and tool design and acquisition support. He also teaches courses in plastics engineering for the University of Arkansas in Little Rock and has made a number of webinars and presentations on plastics processing. Paul holds a number of patents on innovative processes and product designs.
Date de parution : 03-2016
Ouvrage de 320 p.
16x23.6 cm
Thème de Plastics Product Design :
Mots-clés :
design material introduction; materials; plastics; part; history; definition; properties; feedstocks; index; polymers; molecular; thermal properties