Friction Stir Processing for Enhanced Low Temperature Formability A volume in the Friction Stir Welding and Processing Book Series Friction Stir Welding and Processing Series
Auteurs : Smith Christopher B., Mishra Rajiv S.
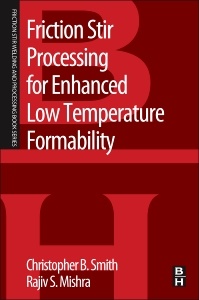
The use of friction stir processing to locally modify the microstructure to enhanced formability has the potential to alter the manufacturing of structural shapes. There is enough research to put together a short monograph detailing the fundamentals and key findings. One example of conventional manufacturing technique for aluminum alloys involves fusion welding of 5XXX series alloys. This can be replaced by friction stir welding, friction stir processing and forming. A major advantage of this switch is the enhanced properties. However qualification of any new process involves a series of tests to prove that material properties of interest in the friction stir welded or processed regions meet or exceed those of the fusion welded region (conventional approach). This book will provide a case study of Al5083 alloy with some additional examples of high strength aluminum alloys.
1. Concept of friction stir processing for enhanced formability2. Fundamentals of formability3. High structural efficiency design potentials with enhanced formability4. Case study of a Al5083 alloy5. Examples of enhanced formability of high strength aluminum alloys6. Closing remarks and guidelines
Researchers, design engineers, materials processing engineers, welding engineers and students
Rajiv S. Mishra is a professor in the Department of Materials Science and Engineering, and Site Director, NSF IUCRC for Friction Stir Processing, at the University of North Texas. Dr. Mishra’s publication record includes 255 papers. Out of these, 10
- Demonstrates how friction stir processing enabled forming can expand the design space by using thick sheet/plate for applications where pieces are joined because of lack of formability
- Opens up new method for manufacturing of structural shapes
- Shows how the process has the potential to lower the cost of a finished structure and enhance the design allowables
Date de parution : 03-2014
Ouvrage de 148 p.
15x22.8 cm