Fault-Diagnosis Applications, 2011 Model-Based Condition Monitoring: Actuators, Drives, Machinery, Plants, Sensors, and Fault-tolerant Systems
Auteur : Isermann Rolf
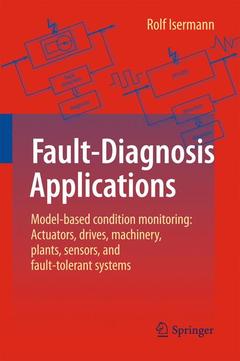
Supervision, condition-monitoring, fault detection, fault diagnosis and fault management play an increasing role for technical processes and vehicles in order to improve reliability, availability, maintenance and lifetime. For safety-related processes fault-tolerant systems with redundancy are required in order to reach comprehensive system integrity.
This book is a sequel of the book ?Fault-Diagnosis Systems? published in 2006, where the basic methods were described. After a short introduction into fault-detection and fault-diagnosis methods the book shows how these methods can be applied for a selection of 20 real technical components and processes as examples, such as:
Electrical drives (DC, AC)
Electrical actuators
Fluidic actuators (hydraulic, pneumatic)
Centrifugal and reciprocating pumps
Pipelines (leak detection)
Industrial robots
Machine tools (main and feed drive, drilling, milling, grinding)
Heat exchangers
Also realized fault-tolerant systems for electrical drives, actuators and sensors are presented.
The book describes why and how the various signal-model-based and process-model-based methods were applied and which experimental results could be achieved. In several cases a combination of different methods was most successful.
The book is dedicated to graduate students of electrical, mechanical, chemical engineering and computer science and for engineers.
1. Introduction
1.1 Process automation and supervision
1.2 Product life cycle and fault management (asset management)
1.3 Contents
I SUPERVISION, FAULT DETECTION AND DIAGNOSIS
2. Supervision, fault detection and fault diagnosis methods
2.1 Basic tasks of supervision
2.2 Terminology
2.2.1 Faults, failures, malfunctions
2.2.2 Reliability, availability, safety
2.2.3 Fault tolerance and redundancy
2.3 Knowledge based fault detection and diagnosis
2.4 Signal based fault detection methods
2.4.1 Limit checking
2.4.2 Trend checking
2.4.3 Change detection
2.4.4 Adaptive thresholds
2.4.5 Plausibility checks
2.4.6 Signal analysis methods
2.5 Processmodel based fault detection methods
2.5.1 Process models and fault modeling
2.5.2 Fault detection with parameter estimation
2.5.3 Fault detection with state observers and state estimation
2.5.4 Fault detection with parity equations
2.5.5 Direct reconstruction of not measurable variables
2.6 Fault diagnosis methods
2.6.1 Classification methods
2.6.2 Inference methods
2.7 Fault detection in closed loops
2.8 Data flow structure for supervision
II DRIVES AND ACTUATORS
3. Fault diagnosis of electrical drives
3.1 Direct current motor (DC)
3.1.1 Structure and models of the DC motor
3.1.2 Fault detection with parity equations
3.1.3 Fault detection with parameter estimation
3.1.4 Experimental results for fault detection
3.1.5 Experimental results for fault diagnosis with SELECT
3.1.6 Conclusions
3.2 Alternating current motor (AC)
3.2.1 Structure and models of induction motors
3.2.2 Signal based fault detection of power electronics
3.2.3 Model based fault detection of an AC motor
3.2.4 Concusions
4. Fault diagnosis of electrical actuators
4.1 Electromagnetic actuator
4.1.1 Position control
4.1.2 Fault detection with parameter estimation
4.2 Electromagnetic automotive throttle valve actuator
4.2.1 Structure and models of the actuator
4.2.2 Input test cycle for quality control
4.2.3 Fault detection with parameter estimation
4.2.4 Fault detection with parity equations
4.2.5 Fault diagnosis
4.2.6 Fault diagnosis equipment
4.2.7 Conclusions
4.3 Brushless DC motor actuator and aircraft cabin pressure valve
4.3.1 Structure and models
4.3.2 Fault detection with parameter estimation
4.3.3 Fault detection with parity equations
4.3.4 Conclusions
5. Fault diagnosis of fluidic actuators
5.1 Hydraulic servo axis
5.1.1 Hydraulic servo axis structure
5.1.2 Faults of hydraulic servo axes
5.1.3 Models of the spool valve and cylinder
5.1.4 Fault detection and diagnosis of the valve and cylinder
5.1.5 Fault diagnosis
5.1.6 Conclusions
5.2 Pneumatic actuators
5.2.1 Pneumatic flow valve structure and modeling
5.2.2 Fault detection and diagnosis with local linear models
5.2.3 Experimental results
5.2.4 Conclusions
III MACHINES AND PLANTS
6. Fault diagnosis of pumps
6.1 Centrifugal pumps
6.1.1 Status of pump supervision and fault detection
6.1.2 Models of a centrifugal pump and pipe system
6.1.3 Fault detection with parameter estimation
6.1.4 Fault detection with nonlinear parity equations and parameter estimation
6.1.5 Conclusions
6.2 Reciprocating pumps
6.2.1 Structure of a diaphragm pump
6.2.2 Models of a diaphragm pump
6.2.3 Fault detection and diagnosis of the hydraulic part
6.2.4 Fault detection of the pump drive
6.2.5 Conclusions
7. Leak diagnosis of pipelines
7.1. Status of pipeline supervision
7.2 Mathematical models of pipelines
7.3 Model based leak detection
7.3.1 Leak detection with state observers
7.3.2 Leak detection with mass balance and correlation analysis for liquid pipelines
7.3.3 Leak detection for gas pipelines
7.4 Experimental results
7.4.1 Gasoline pipeline
7.4.2 Gas pipeline
7.4.3 Conclusions
8. Fault diagnosis of industrial robots
8.1 Structure of a 6-axis robot
8.2 Model af a robot axis
8.3 Fault detection and diagnosis with parameter estimation
8.4 Experimental results
8.5 Conclusions
9. Fault diagnosis of machine tools
9.1 Structure of machine tools
9.2 Status of machine tool supervision
9.3 Main drive
9.4 Feed drive
9.5 Drilling machine
9.3.1 Models of the drilling process
9.3.2 Fault detection of drilling
9.6 Milling machine
9.6.1 Models of the milling process
9.6.2 Fault detection of the cutter
9.7 Grinding machine
9.7.1 Grinding process and models
9.7.2 Fault detection with parameter estimation
9.7.3 Fault detection with signal analysis methods
9.8 Conclusions
10. Fault detection of heat exchangers
10.1 Heat exchangers and their models
10.1.1 Heat exchanger types
10.1.2 Heat exchanger models for stationary behavior
10.1.3 Dynamic models of heated tubes
10.2 Fault detection from static behaviour
10.2.1 Static models of heat exchangers
10.2.2 Fault detection methods
10.3 Fault detection of a steam/water heat exchanger with dynamic models and parameter estimation
10.4 Fault detection for a double heat exchanger plant with local linear neuro-fuzzy models
10.4.1 Steam-water heat exchanger with local linear identification
10.4.2 Heat exchanger plant
10.4.3 Fault detection with multiple local linear parameter estimation
10.5 Conclusions
IV FAULT TOLERANT SYSTEMS
11. Fault-tolerant systems – a short introduction
11.1 Basic redundant structures
11.2 Degradation steps
12. Examples of fault-tolerant systems
12.1 A fault-tolerant control system
12.2 Fault-tolerant electrical drives
12.3 Fault-tolerant actuators
12.4 Fault-tolerant sensors
V APPENDIX
13. Terminology for fault detection and diagnosis
References
Index
Presents applications of modern fault diagnosis to technical systems
Written by one of the most distinguished expert in this field
Focuses on selected topics
Includes supplementary material: sn.pub/extras
Date de parution : 11-2014
Ouvrage de 354 p.
15.5x23.5 cm
Date de parution : 04-2011
Ouvrage de 354 p.
15.5x23.5 cm